Mr. Hirschfeld, suppose you had to give version 10.0 a title: What would it be?
Flemming Hirschfeld: At the IPA annual conference in November 2023, the title of the TechTalk was “Simply more ERP”. Perhaps one or two participants will remember that. In any case, the title of the talk sums it up well. Much of what is hidden in version 10 is simply pure ERP functionality that makes life easier for manufacturing companies.
Simplification sounds promising. In your opinion, which three innovations in the areas of functionality and technology particularly contribute to this idea?
At the top of the list, of course, is the modularization and provision of PSIpenta/ERP on the group-wide Java platform. This brings with it a whole range of advantages. Among other things, we guarantee operational and platform independence. Splitting the ERP system into modules also simplifies several issues, such as the installation and configuration of solution modules, as well as deployment, updates and operation. In second place, I see the topic of cross-structure material scheduling and picking, and in third place for me are the blanket production orders.
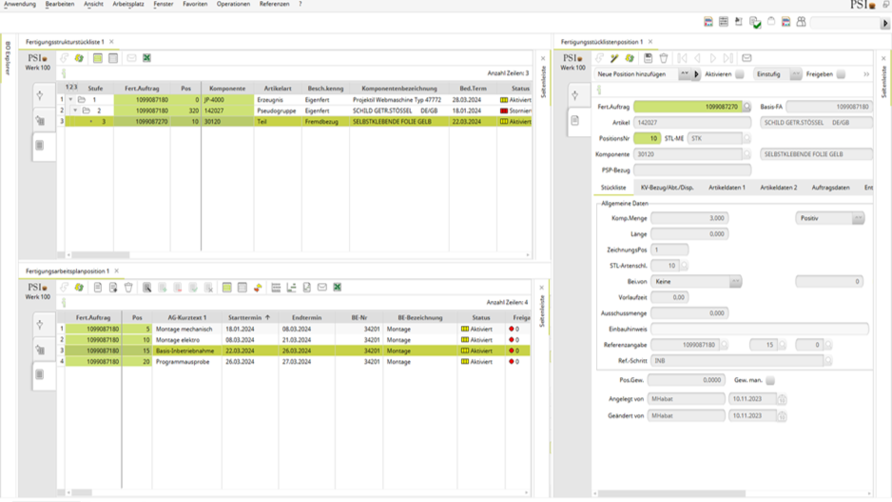
Let's first take a closer look at the topic of material scheduling and picking. What is new in this area in version 10 and why is it in the context of simplification?
Let me start by saying that this topic - just like the following one - was developed in close cooperation with customers. So both originated in a project, were then further developed in an IPA working group and thus made it into the standard.
So from practice for practice.
Absolutely. It is simply important to me to show that we don't just talk about it. We really live this philosophy. In cross-structure material scheduling and picking, we take up the fact that parts lists are generally created in the design department. Their structure, as well as the derivation of dates in the ERP system, has so far followed this design logic - in simple terms “from top to bottom”.
From a production perspective, however, this structure rarely corresponds to the necessary processing sequence. If, for example, components need to be processed earlier in some form or can be moved to final assembly, companies maintain a productive bill of materials in parallel to the constructive one. This works, but it is also easier. In version 10, a structure is now automatically generated that is suitable for assembly, i.e. material and picking are precisely coordinated and synchronized across structures. This simplifies planning and saves considerable time and effort.
PSIpenta/ERP 10.0 - Highlights at a glance
Takt is a good keyword to transition to the frame production orders for series manufacturers. Can you also shed some light on this function and explain how it relates to simplification?
Let's take a brief look at the typical processes of a supplier. As a rule, they call off customer requirements via EDI every few days or, in case of doubt, even daily, and control their production using a batch size procedure. This means that the delivery call-offs are summarized in a practicable production lot size. The ERP system generates a production order including a confirmation number for each EDI call-off. This production order forms the planning basis and generates all requirements. Particularly in the case of large orders, many orders are created at short intervals, which are always the same and yet must always be checked, released and posted correctly. This is exactly where the blanket production order comes in. From version 10, companies can create such an order for a specific quantity, e.g. monthly. This is not effective for planning purposes, but only forms a kind of bracket around the call-offs from a higher-level sales order and the production orders generated from it.
What is EDI (Electronic Data Interchange)?
Electronic Data Interchange (EDI) is the computer-to-computer exchange of business documents in a standard electronic format between business partners.
By moving from a paper-based exchange of business document to one that is electronic, businesses enjoy major benefits such as reduced cost, increased processing speed, reduced errors and improved relationships with business partners. Source: EDI basics
So it's basically a kind of administrative trick to streamline and simplify production processes?
A small trick, but with a big effect - you could say that. The concrete advantage is that employees in production no longer have to select and post the individual and correct production orders, but rather the higher-level blanket production order. This minimizes sources of error, speeds up processes and is, of course, much simpler. Above all, because nothing changes to the higher-level logic in the ERP system.