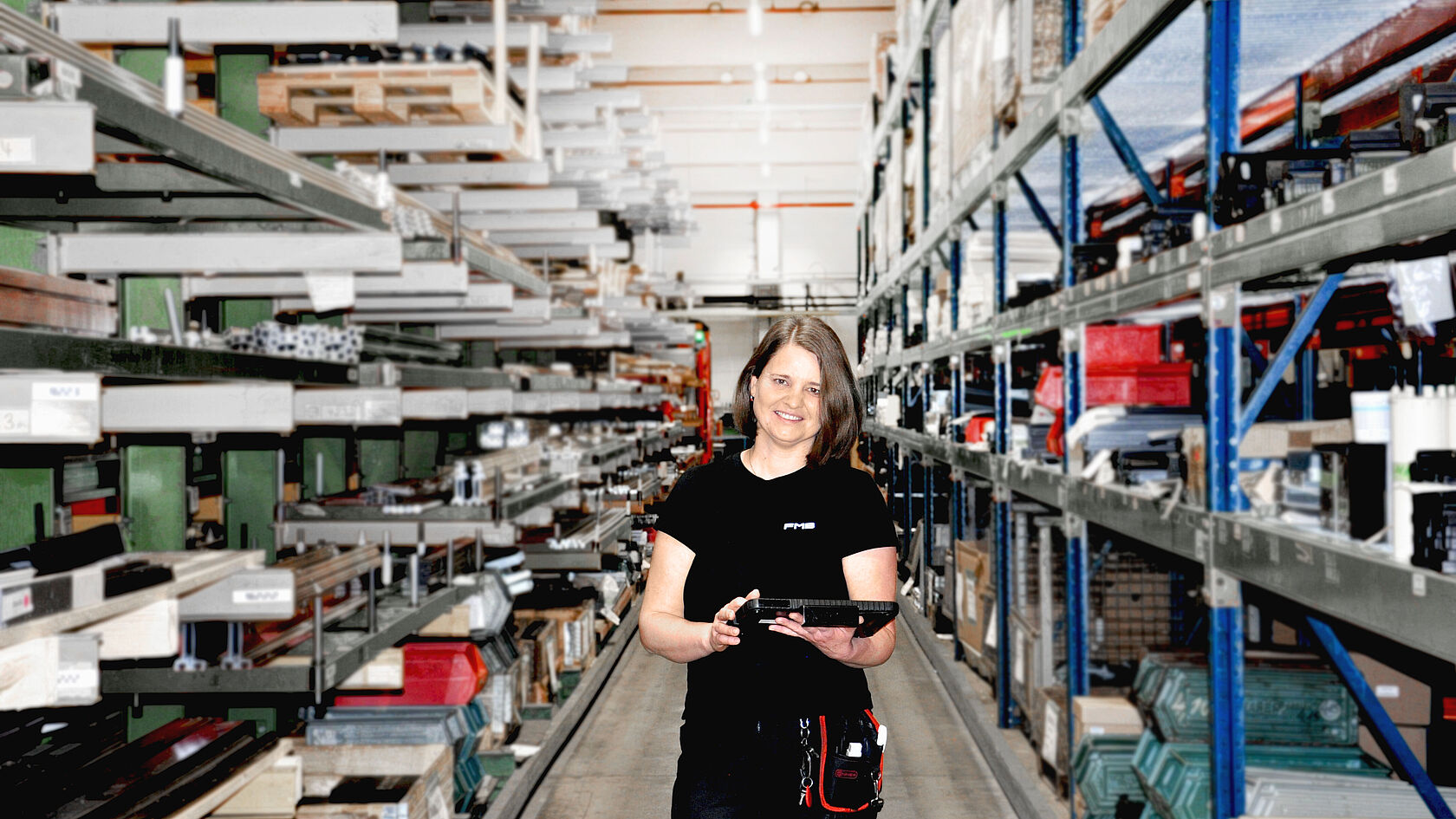
Case Study With PSIpenta/ERP and industrial app: FMB accelerates picking processes
In the course of process optimization, FMB Maschinenbaugesellschaft also took a close look at its picking processes for assembly and completely digitized them using an ERP system and an app. Picking is now twice as fast as before.
With the introduction of the PSIpenta industrial app, FMB Maschinenbaugesellschaft has significantly improved its picking processes for assembly. Route-optimized material removal, direct posting in PSIpenta/ERP and an improved storage system on the transport trolleys save up to 50 percent time in picking and up to 30 minutes in assembly per order.
About FMB Maschinenbaugesellschaft
FMB Maschinenbaugesellschaft specializes in automation solutions for loading and unloading machine tools. The company from Lower Franconia has delivered more than 29,000 loading magazines and handling systems.
Challenges
In recent years, the requirements and therefore the complexity of loading magazines have increased continuously. Each magazine can consist of up to 300 individual parts and pre-assembled modules. This development requires adjustments in the planning and organization of production and assembly as well as in the supporting IT systems.
In order picking for assembly or flow production without shift operation, the parts lists generated in PSIpenta/ERP were also created in material tables and made available to the pickers via tablets. The employees retrieved the required parts from the warehouse according to the table, ticked them off in the list and placed them loose on a trolley for each order.
Posting to the ERP system was done later on the PC. For accessories such as telescopic tubes, adapter sets or conversion kits, a replacement document was also created and printed. "These processes took a lot of time, both in the removal and in the allocation in the assembly, were prone to errors here and there, and ultimately were no longer state-of-the-art," says Claudia Karl, ERP representative at FMB.
Production features
- Flow production without shift operation
- Production and assembly of 3 to 4 loading magazines per day
- Parts lists with 180 to 300 individual parts per system
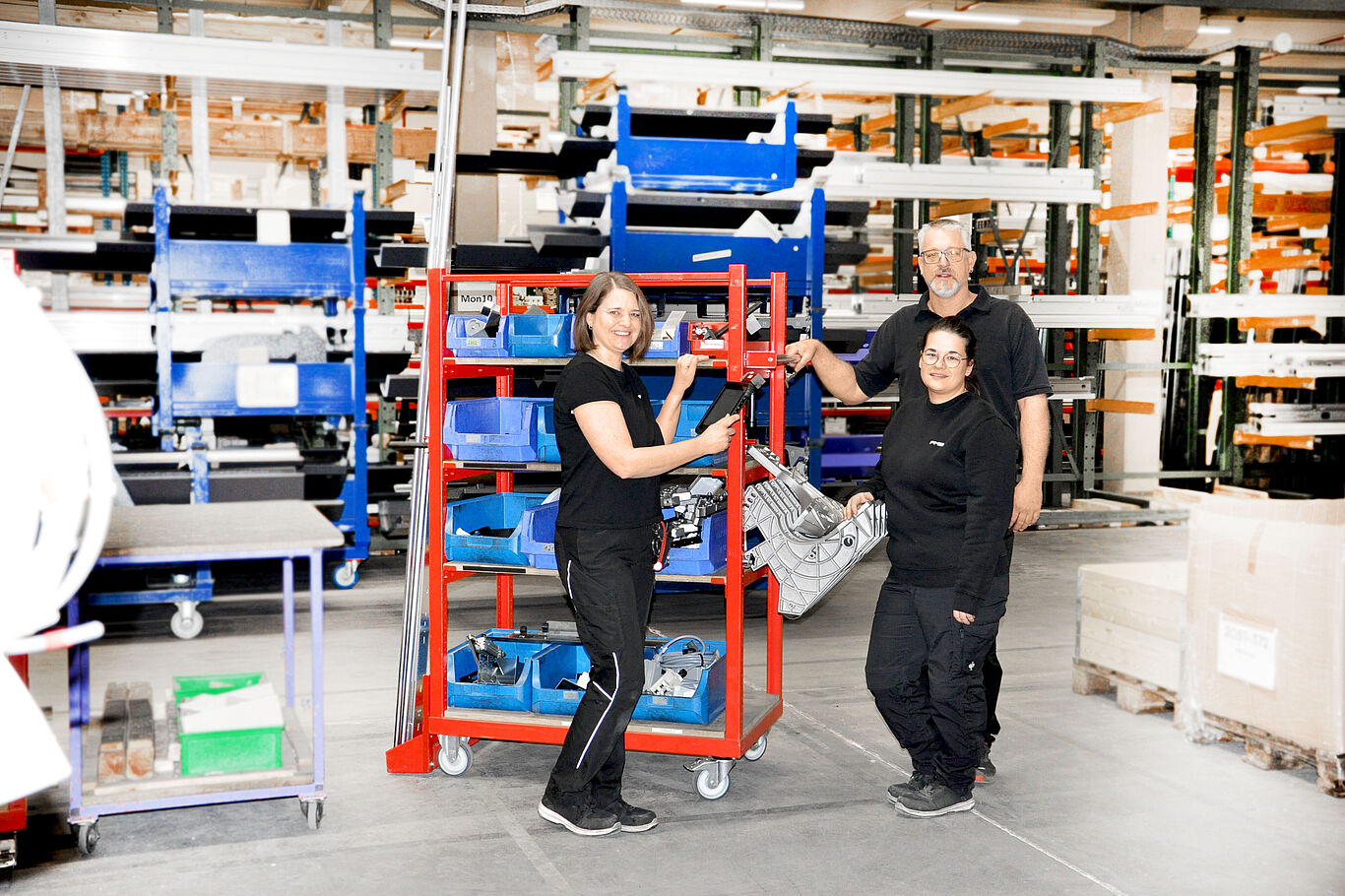
Objectives
FMB wanted to make its picking processes more efficient in order to achieve short throughput times despite the increasing complexity of the loading magazines and handling systems and thus continue to be able to offer fast delivery times. Among other things, the focus was on the seamless digitalization of data capture and the optimized provision of the required parts for assembly.
The most important goals
- Digital transformation in order picking
- Picking without manual intermediate steps via a single system
- Reduction in material removal and picking times
- Direct data posting to the ERP system
- Optimized provision of parts for assembly
Solution approach
With the introduction of the PSIpenta industrial app, pickers can post all data directly into PSIpenta/ERP via a tablet. In combination with a route-optimized picking list and a brewing group-oriented storage logic, the entire picking process has been digitized and made more efficient.
If a part is not in stock, this information is also entered directly into the app, and the system automatically creates a missing parts list after picking is complete. Fast-moving items, such as nuts and screws, that are located directly at the assembly station are automatically booked as soon as the assembly order is released.
FMB has also optimized the storage system on the trolleys, which now uses containers for each assembly. The container logic is determined by clicking in the app and when a new machine is commissioned. The system determines the container sizes for each assembly and writes them to the appropriate work order BOM line. Sometimes designers enter the appropriate size specifications based on experience with existing assemblies. Pickers then sort the parts into appropriately sized and numbered containers for each assembly. A container list is created for each customer transaction.
The result
Thanks to process optimization, FMB was able to halve the time required for material picking. In assembly, the clearly laid out storage system saves up to 30 minutes per order – not least because the automated missing parts lists prevent and minimize downtime. This enables smooth flow production with up to four machines per day – without the need for shift work.
- 50 percent time savings in picking
- Up to 30 minutes assembly time savings per order
- Minimized downtime with automated missing parts lists
- 100% adherence to planned cycle time for up to four machines per day
- Inventory accuracy in the ERP system
- Delivery reliability and planning certainty for FMB customers
Thanks to the app-controlled, route-optimized material removal, the storage of individual parts by assembly in containers, and the direct posting in the ERP system, FMB has reduced the time required for this from up to three hours to a maximum of 1.5 hours (a 50% reduction). During assembly, the new storage system saves up to 30 minutes per order. As a result, FMB can fully meet the planned cycle times of three to four machines per day in flow production without shift work.
Conclusion
Route optimization, real-time data collection and systematic filing logic: FMB has accelerated processes, reduced employee workload and ensured production goals by efficiently redesigning and seamlessly digitizing the picking process with PSIpenta/ERP and industrial app.