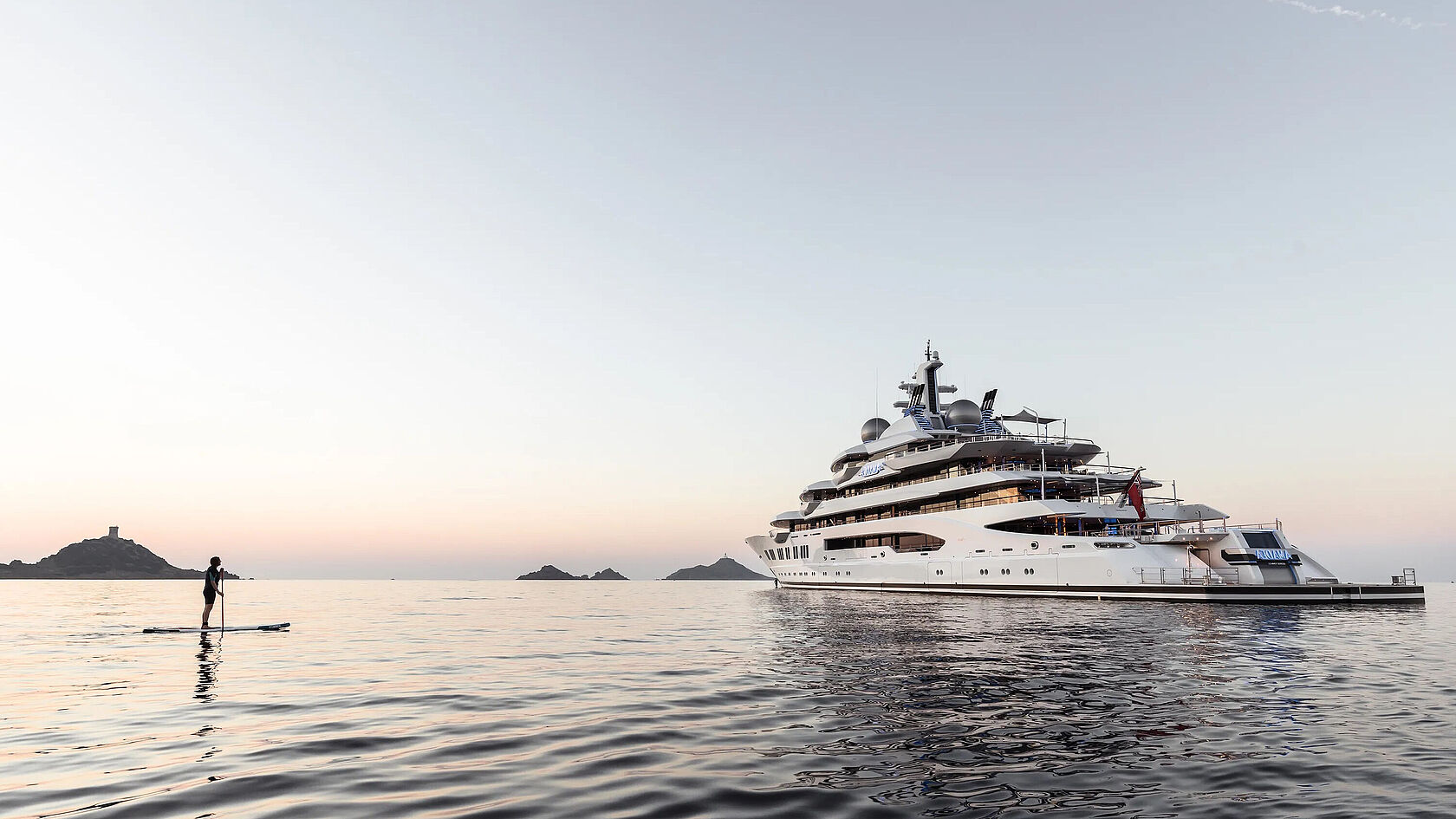
Case Study Lürssen steers yacht construction in a new ERP standard
The shipyard from northern Germany uses PSI's ERP and MES solutions to map complex project structures.
Decades of experience pay off: The Lürssen shipyard in Schleswig-Holstein has always been very popular with buyers of mega yachts. The north Germans have truly earned their good reputation, because despite demanding planning and implementation, the shipyard consistently delivers yachts of the highest quality - on time and worldwide. To ensure that it can continue to do so, the shipyard migrated to the latest version of PSIpenta/ERP and remained in the standard.
About Lürssen
“Nothing is impossible” is the guiding principle at the Lürssen-Kröger shipyard (Lürssen), which has allowed the family business to continuously set new standards in shipbuilding and, increasingly, in yacht building since it was founded in 1875. Many of the largest and most technologically sophisticated yachts in the world come from the traditional company, which now has a total of eight shipyards.
It takes about three years of construction before a yacht is launched; Lürssen delivers just under two ships each year. The “Azzam”, for example, is one of the largest motor yachts ever built: it measures 181 meters, weighs over 13,000 tons and is packed with highly developed technology.
The Lürssen engineers will implement any customer request, regardless of the effort involved.
Challenges
Project and custom manufacturing at Lürssen requires complex project structures to be planned. Before migrating to the latest PSIpenta version, it was clear that these should be mapped as closely as possible to the ERP standard in the new system. At the same time, a number of special features were to be implemented, such as the lack of delivery notes, a quick goods entry mask for the quick transfer of large quantities of goods to the warehouse, and an order set function for items with long lead times.
Production characteristics
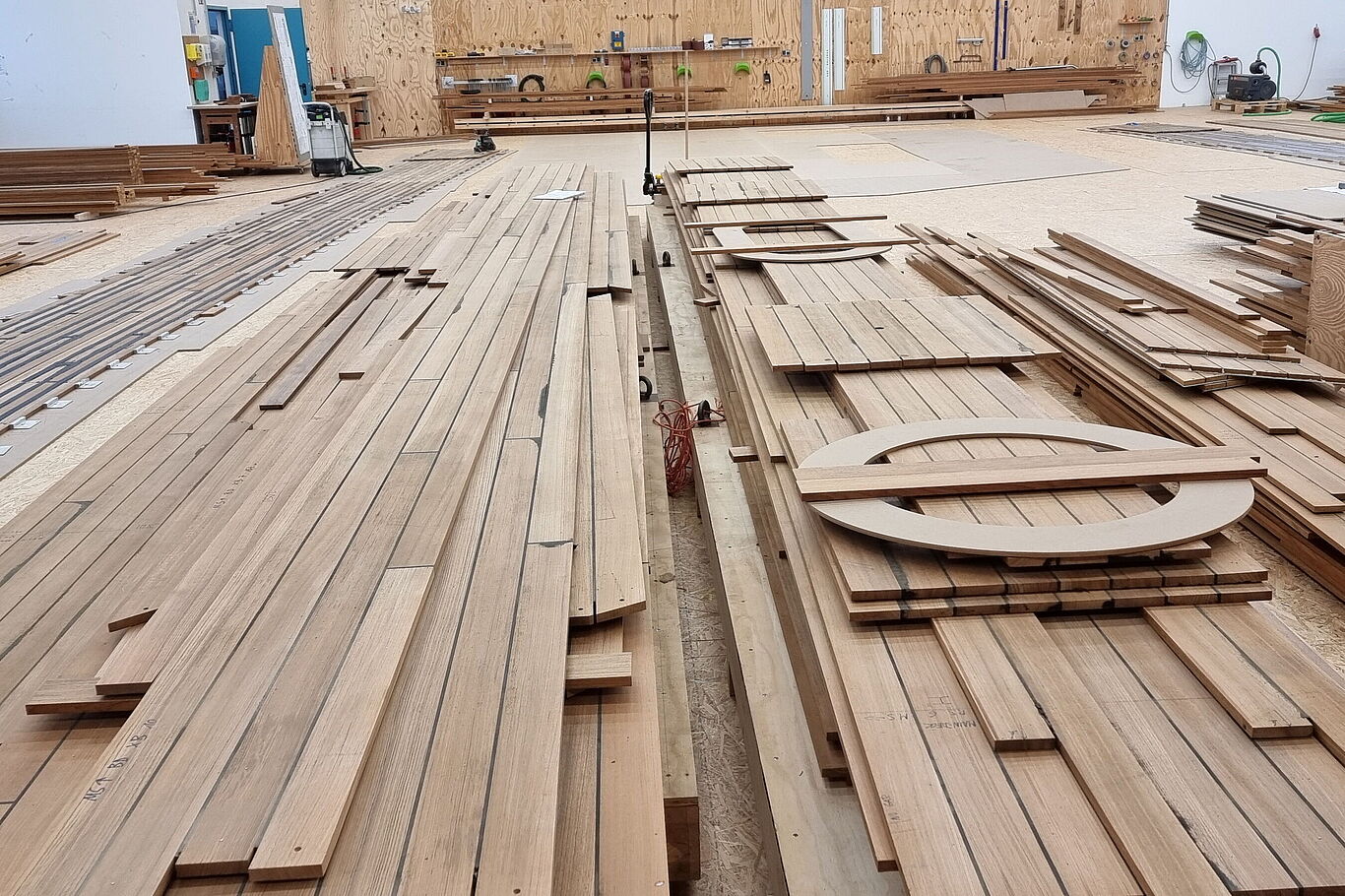
Objectives
By switching from the highly customized ERP version to the latest, Java-based version of PSIpenta/ERP, the company wanted to benefit from technological and functional advantages, including the ability to react flexibly to structural changes and to map process-oriented and thus transparent project structures. At the same time, Lürssen aimed to harmonize structures between design and production and to ensure updateability by implementing all requirements in the ERP standard to the greatest possible extent.
The main objectives
- Mapping of process-oriented project structures
- Harmonization of the structures of design and manufacturing
- Increase in process and project transparency
- ERP update capability through the greatest possible approximation to the system standard
Approach
The main reason for the migration was a process redesign, primarily to more closely link the previously quite autonomous structures of design and manufacturing. “Design engineers are accustomed to thinking in systems,” says IT manager Lothar Brose, describing the differences. ‘On the other hand, production planning is process-oriented in various construction phases – each summarized in several major milestones.’ The project structures module was also to be installed as a central element.
Design engineers are accustomed to thinking in systems. On the other hand, production planning is process-oriented in various construction phases – each summarized in several major milestones.
Realization
In order to link design and production more closely, the designers are now using the latest ERP version to develop a non-effective parts list for the respective systems, which also contains all other relevant information. This includes, in particular, the value flow for the respective project. Once a designer has finalized a parts list, it is transferred to the work preparation stage. “From the left-hand side – which is the design view for us – an employee moves it to the right-hand side, and thus to the production side, using drag and drop – and into one or more parts lists that are effective in terms of materials planning,” explains Brose. Project planning automatically assigns work packages to these newly created parts lists, which also contain the time horizon for the respective part, and optimizes them. In addition, the system establishes a relationship between the left and right sides, which means that if changes are made in the design view, the necessary shifts on the production side are immediately apparent.
By using PSIpenta/project structures, a project plan can comprise up to 11,000 items. This allows Lürssen to map all relevant planning items. The system transmits these as work packages to the order management via an interface. This automatically generates the corresponding production order structures, including a timeline and work package numbers. Lürssen uses this as a basis to flexibly and efficiently control production, maintain an overview of the processing statuses and respond to events in a timely manner.
The result
80 percent of it in the standard ERP
Eighty percent of the standard system instead of a highly customized system: Lürssen has achieved its ambitious goal for mega-yacht construction. It was crucial for the shipbuilder that it was fully operational from day one, despite the special scope of the project.
Although the long duration of the project means that it is not yet possible to express the effects of the ERP migration and process redesign in figures, it is already clear that the company has a high level of transparency across all processes, that the planning and ordering of components has been significantly optimized, and that production can be controlled flexibly and efficiently.
Conclusion
Flexible, precise and transparent processes despite highly complex project structures in yacht building – Lürssen must be able to rely on them. By migrating to the latest version of PSIpenta/ERP and using project management, the company has achieved precisely that. Lürssen also expects a leap in quality with the introduction of the PSIpenta /Industrial App for warehouse management. Its integration is already on the IT manager's to-do list.