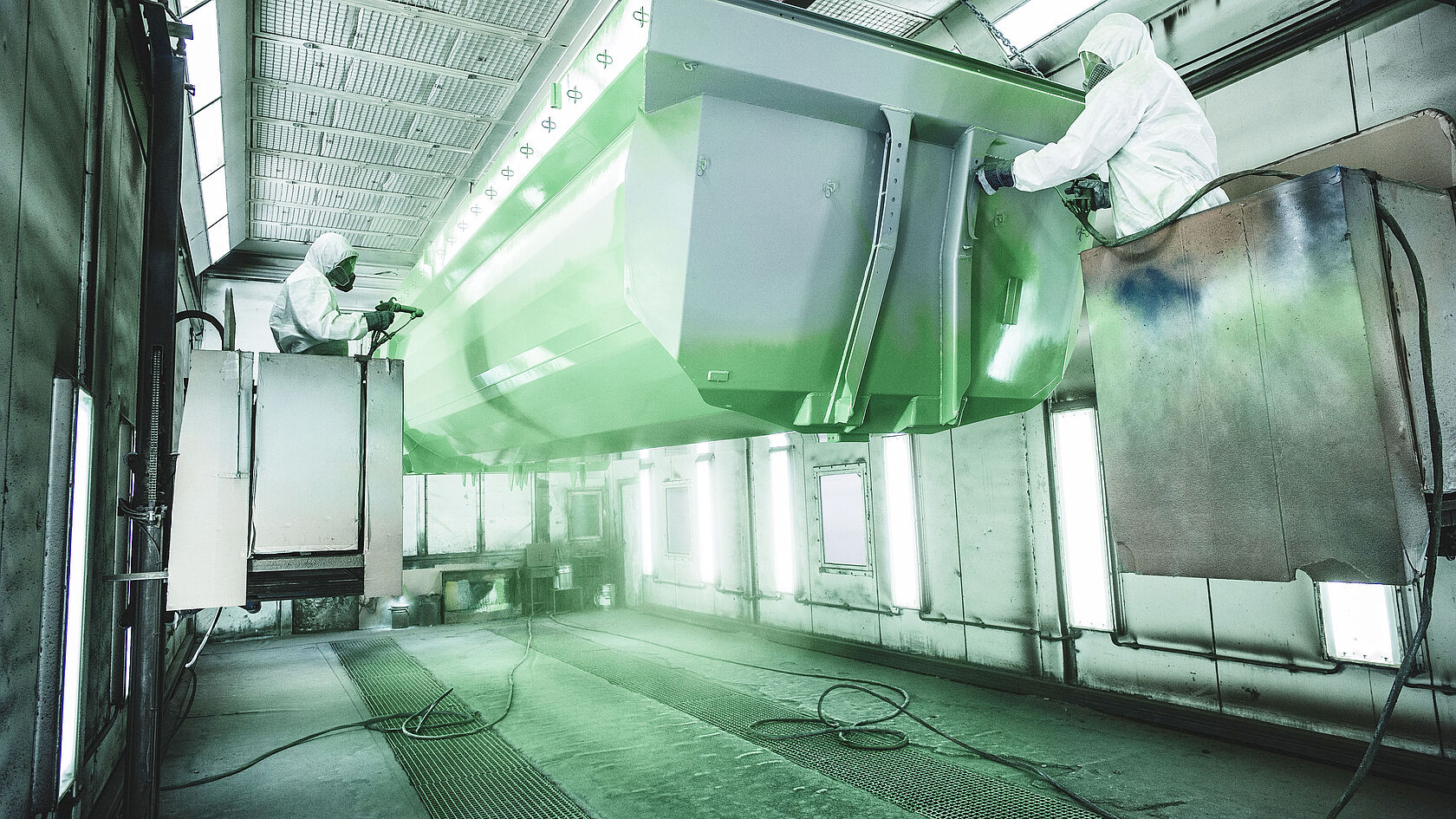
Case Study Automated multisite solution increases flexibility and efficiency
Wilhelm Schwarzmüller GmbH optimizes cross-location processes with PSI's ERP and MES solutions.
The Austrian company, an international full-service provider of commercial vehicles, has sophisticated organizational structures. By using PSIpenta/ERP and PSIpenta/MES, Schwarzmüller is creating efficient, integrated processes and benefiting from a uniform database.
About Wilhelm Schwarzmüller
Wilhelm Schwarzmüller GmbH (Schwarzmüller) is one of Europe's largest full-service providers of towed commercial vehicles, in particular for long-distance transport, the construction industry, and the waste disposal and petroleum industries. Approximately 2,300 employees work in production facilities in Austria, the Czech Republic and Hungary, as well as in repair shops, sales and partner locations in over 20 countries in Central and Eastern Europe.
Challenges
As a full-service provider, the Austrian company not only develops and produces commercial vehicles. Schwarzmüller also maintains a large service network, trades in spare parts and rents out vehicles for a wide range of applications. In the production area, Schwarzmüller manufactures according to industrial standards and at the same time offers a very high level of diversity: the company can produce 135 vehicle types in approximately 1,000 variants.
Production characteristics
- Sophisticated cross-plant and cross-location business processes
- Orchestration of production, service, spare parts and vehicle rental in 20 countries
- Production according to industrial standards despite a high proportion of customized products
- High diversity: production of 135 vehicle types in approx. 1,000 variants
- Complex planning requirements
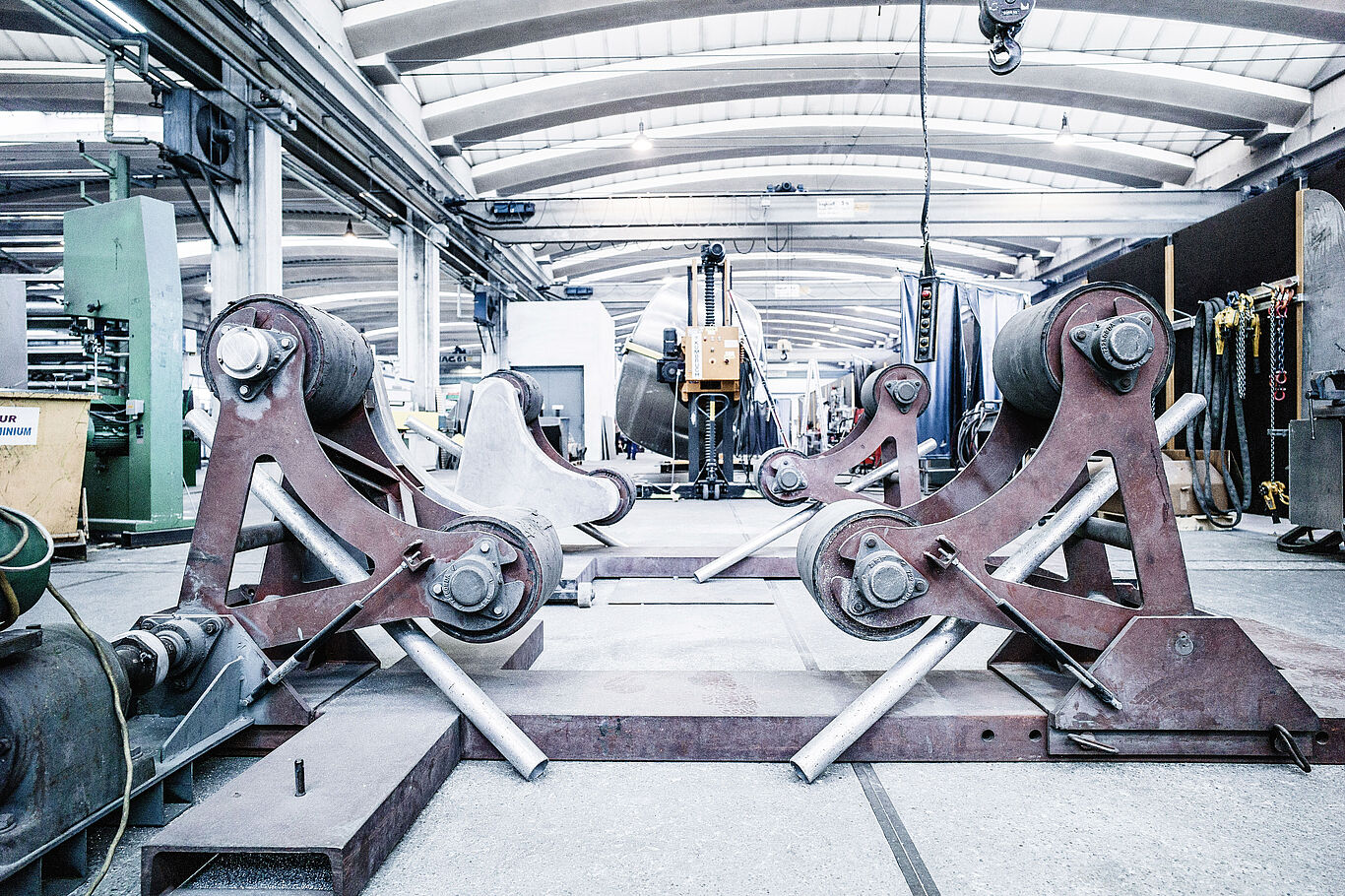
Objectives
The main goal of the ERP implementation was to harmonize the production and logistics processes in the various plants and to achieve a high level of availability and efficiency across all locations on a permanent basis. To achieve this goal, Schwarzmüller's IT specialists were looking for a software that would support the complex company structure, including services, sales and procurement, in order to establish optimized processes across plants and countries and to ensure efficient production.
The main objectives
- Mapping of the complex, international multi-plant structure, including various languages, currencies and authorizations
- Support for processes in all business areas
- Central control of production processes across plant and country borders
- Efficient mapping of the high number of variants
- Standardization of the database for fast reporting
Approach
In addition to the PSIpenta/ERP base system, the PSIpenta/Multisite module for controlling multiple plants plays a particularly important role at Schwarzmüller. Four language versions and currencies are used: German, English, Czech and Hungarian, as well as euros, crowns, forints and lei.
Realization
PSIpenta/ERP maps all of Schwarzmüller's company processes, from incoming orders to invoicing, and is installed with a full range of functions at eleven sites. Schwarzmüller manages cross-plant business processes and shared data using “Multisite” and controls them from the central installation in Freinberg. All relevant information is available at a glance and forms the basis for reliable statements regarding the availability and scheduling of the requested deliveries. When the CRM system reports an incoming order to the ERP system, the customer's location determines the plant that is creating the order, which then also takes over the invoicing.
Standardized interfaces for seamless processes
The company also realizes enormous potential through the easy-to-use standard interfaces and the resulting process consistency, for example, with the CRM system or for financial accounting. The same applies to the integration of production machines into the ERP system, such as laser cutting and bending machines. These receive the production order, including the CAD drawing, from the ERP system and report back to the ERP system when the job is complete.
The result
Centralized control increases efficiency and transparency
Thanks to the central multisite control, Schwarzmüller can harmonize and efficiently coordinate production and other services across plant and national borders.
Conclusion
As an international company, Schwarzmüller uses PSIpenta/ERP and PSIpenta/MES to map its sometimes complex structures consistently and benefit from optimized, efficient processes. By using the multi-site control, Schwarzmüller can rely on a uniform and solid database that creates the basis for successful company management.