Logistics simulation is essential to modern warehouse environments. They enable companies to anticipate risks, identify bottlenecks, and uncover opportunities for optimization - without disrupting operations or incurring additional costs. Using automated testing or AI-driven methods, companies can realistically model complex workflows and test different scenarios. This enables data-driven decisions that improve efficiency and resilience. In this article, we explain how simulations can help optimize logistics processes for the long-term.
What is logistics simulation?
Simulations are a powerful tool in logistics for realistically mapping and analyzing complex processes and their interactions. This technology can be used to visualize processes, identify bottlenecks and test alternative scenarios without affecting ongoing operations.
Logistics simulation maps real-world processes like warehousing, transportation, and manufacturing in a controlled, digital environment. This allows the effects of changes in one area (e.g. stock levels or route planning) on other parts of the logistics chain to be determined and optimized without risk.
Advantages of simulation
The advantages of simulating logistics processes go far beyond simply improving efficiency. In an increasingly interconnected global economy, supply chains and logistics processes are often characterized by fluctuations and uncertainties, such as demand and resource availability. Simulation can help companies address these challenges and optimize their logistics processes.
Advantages at a glance:
- Cost and risk reduction: Costly errors can be avoided through preventative analysis. Logistics simulation allows you to identify potential bottlenecks or inefficient processes early and correct them before they become real problems.
- Increasing process reliability: Simulations help identify weaknesses and potential risks. As a result, companies can improve process reliability and ensure that processes run smoothly even under unforeseen conditions.
- Flexibility and adaptability: Simulations enable flexible response to changing market demands or external disruptions. Companies can run through different scenarios - such as fluctuating demand, delivery delays, or resource bottlenecks - and develop the best strategies for each.
- Data-based decision-making: Simulations provide a solid foundation for strategic decisions. The insights gained make logistics processes more transparent and help management make informed, risk-based decisions.
Automated testing in logistics
Simulations supported by automated testing are becoming increasingly important in logistics. They enable fast and thorough testing of changes to the warehouse management system (WMS) without the need for time-consuming manual testing. Especially when users have made changes to their intralogistics or when a new release is available, they should be able to test their system. Automated test suites offer significant advantages.
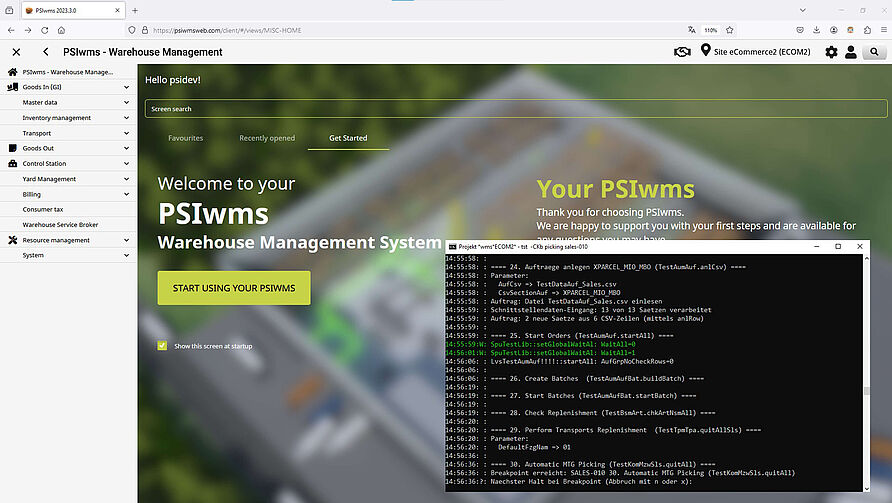
Advantages of automated testing
Compared to manual procedures, automated testing is faster, more accurate and more adaptable. Automated testing in a WMS tests physical or software-based processes for functionality and accuracy. Test cases (also known as test suits) cover different scenarios such as incoming goods, outgoing goods, picking strategies, or special cases such as cross-docking. This allows large volumes of data to be tested quickly and repeatedly. The goal is to ensure that all processes run correctly without the need for human intervention. Automated processes offer many advantages over manual testing.
Advantages at a glance:
- Test scripts run automatically
- Reproducible and complete test sequences
- Minimal programming knowledge required
- Documentation of test results
- Customer saves time and money by avoiding errors
- Improved software quality and transparent project status
- High security for updates to productive systems
- Test protocols are available for acceptance tests
- Project progress can be evaluated with passed tests
From the field: FIEGE and NOSTA
Despite all the advantages, manual testing will not become completely obsolete, as it still has its place, especially for specialized customizations to the system. Nevertheless, manual testing will be pushed back more and more in the coming years, as the advantages of the automated process clearly outweigh the disadvantages. For this reason, PSI has integrated a test framework into its PSIwms, which is designed for the simulation of warehouse processes and enables automated testing - without the need for programming knowledge.
FIEGE, one of the largest logistics service providers in Europe, optimizes the value chains of its customers across all industries with modular concepts. FIEGE controls its intralogistics processes with PSIwms. The automated test tool simplifies the testing of changes in the WMS, saves time and requires less personnel. The logistics specialists from Greven have also had positive experiences with the implementation of new customers. If something is optimized for new customers in an existing multi-user warehouse, this can potentially have a negative impact on existing customers. With automated testing, unwanted interactions can be identified and errors avoided right from the start. The additional testing software gives PSIwms a competitive advantage over other WMS solutions.
The NOSTA Group, a family-owned logistics service provider with 800 employees, has also been using PSIwms since 2008. The company uses the WMS at its seven warehouse locations and benefits from the switch to automated processes. Prior to the implementation of PSIwms, goods receipts and tests were mainly carried out manually, which led to errors and intransparent inventories. Today, automated testing in PSIwms allows NOSTA to non-invasively check whether new customers affect existing processes. Errors can also be detected and corrected at an early stage.
AI in logistics
In addition to automated testing, AI-based methods are becoming increasingly important in logistics. Artificial intelligence offers new opportunities to make logistics processes more efficient and flexible, thereby increasing competitiveness. In the dynamic world of logistics, speed and process quality are critical success factors, as errors can quickly lead to high costs. Artificial intelligence has therefore been considered a key technology in the industry for several years.
Although AI applications are still sporadically used in logistics, for example in the form of chatbots, there are already advanced solutions in the area of warehouse management. One example is PSIwms AI, which was developed specifically to optimize intralogistics.
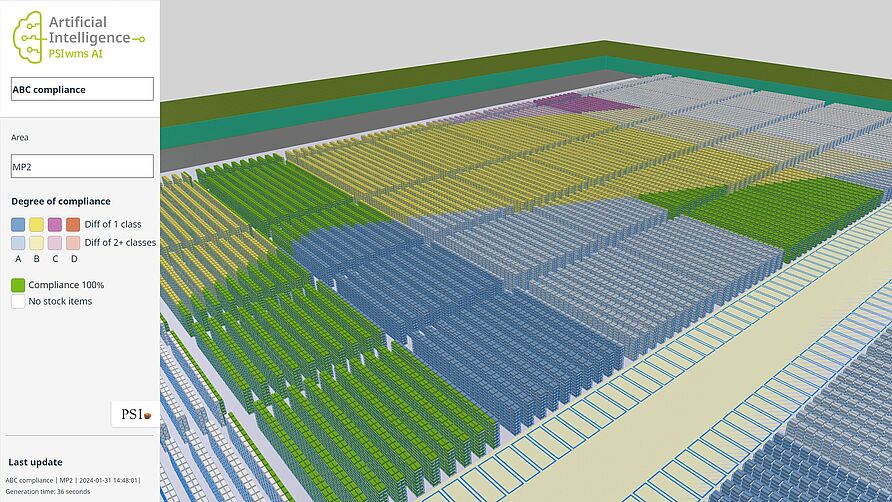
From the field: PSIwms AI
PSIwms AI is an innovative platform developed by WMS specialist PSI for the real-time optimization of warehouse processes. This AI-based solution integrates seamlessly into the warehouse management system and continuously analyzes all warehouse processes to identify optimization potential. A digital twin of the warehouse, which mirrors all real processes, serves as a virtual simulator for testing different scenarios. This simulator generates training data for machine learning models that contribute to the continuous optimization of the system.
Unlike other AI solutions, PSIwms AI does not require manual integration, minimizing sources of error and supporting continuous improvement and increased efficiency in warehouse management.
Advantages of artificial intelligence in intralogistics - Find out more.
Why are simulations important in modern logistics?
In an increasingly dynamic and competitive business world, the efficiency of logistics processes is becoming a critical success factor for companies. Logistics simulation plays a key role in this by allowing complex processes to be tested and optimized without risk and by identifying bottlenecks and inefficiencies early on. Companies simulate different scenarios - such as fluctuating demand or resource shortages - and are better prepared for unexpected changes. Logistics simulation can significantly optimize logistics processes.
What areas of application are logistics simulations suitable for?
Logistics simulations are versatile and are particularly useful in areas such as warehouse management, production planning, transportation logistics, and supply chain management. They help design optimal warehouse layouts, plan transportation routes, and manage stocks efficiently. Simulations are also a valuable tool when introducing new technologies or restructuring operations to analyze potential impacts in advance and make the process as smooth as possible.
How time-consuming is the implementation of a logistics simulation?
The cost of implementing a logistics simulation can vary depending on the scope and complexity of the processes to be simulated. For simpler processes or limited applications, a simulation can often be created and integrated with little effort. However, more complex simulations, such as those for extensive warehouse or supply chain networks, require thorough data preparation and coordination with existing systems, which can take more time and resources. In general, the investment in implementation usually pays off quickly through optimized processes and long-term savings.