Running a metals plant means to manage a variety of interactions between many options. Hundreds of decisions based on production data, reports and Key Performance Indicators (KPIs) have to be made daily by different stake holders. Production planning expert Robert Jäger introduces a practical approach and a supporting tool for planners to help with these tasks.
TechTalks on KPI driven production planning
Steel and aluminum production planning: 3 steps to a successful production plan
Fundamentally, in order to achieve an optimal production plan the metal producer has to apply the three-step-approach:
- Step 1: Business goals definition
- Step 2: Strategy and positioning description
- Step 3: Be agile!
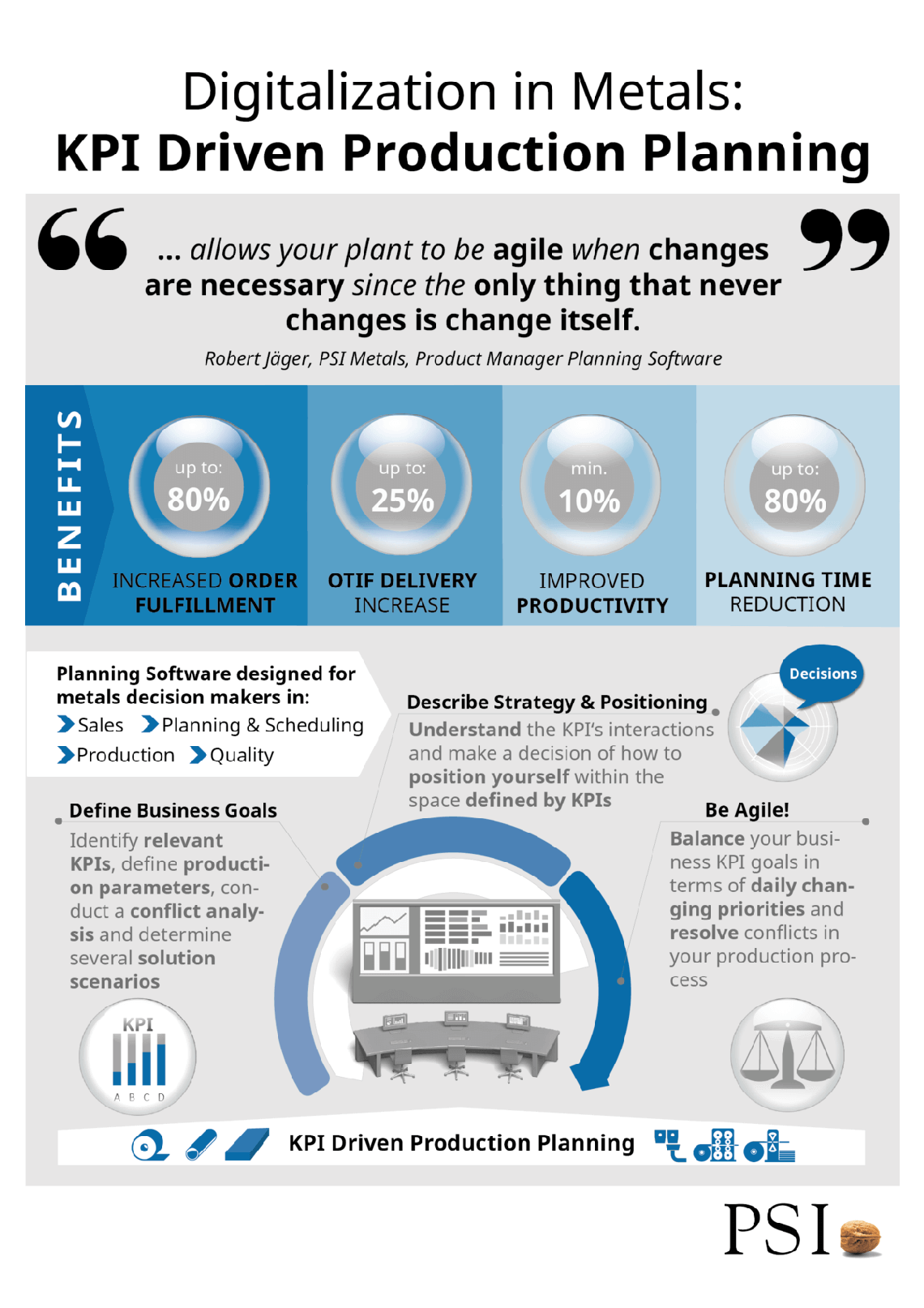
Step 1: Business goals definition
The definition of business goals is the first and probably the most important step on the way to the optimal production plan. In a metal plant, common business goals are usually translated into the so-called Key Performance Indicators, by which the quality of plans or schedules is measured. These include on time in full delivery, capacity utilization and inventory performance.
Consequently, each plant must identify relevant KPIs for its specific supply chain conditions and precisely define the formula for measuring them. By defining these production parameters, objectives for KPI quality assessment can be set.
Step 2: Strategy and positioning description
While some KPIs go hand in hand, others go in opposite directions and are therefore in conflict with each other. Thus, the second step is to understand how these KPIs interact with each other and make a decision about how to position oneself strategically in the space defined by these KPIs.
Step 3: Be agile!
The only thing that never changes is change itself and at some point you will be facing new conditions such as new market situations, new competitors, and so on. The third step on the way to an optimal production plan is therefore agility! By facing change, you must be able to reassess the relative priorities between your goals and sometimes even review the goals themselves.
How to implement this production planning approach
To implement such a three-step approach, you need a supporting tool that helps you to be flexible when changes are needed. This system would help you to define, calculate and analyze KPIs in a user-friendly way. Moreover, it would support you in visualizing the interactions and conflicts of existing KPIs and enable you to carry out simulations.
At PSI we call this approach - KPI-driven production planning. It enables the optimization of plans and schedules based on dynamic business objectives that cover the entire life cycle from sales and production orders to the finished product at all stages of the metal production process. Its high degree of automation with tried-and-tested algorithms ensures that complex planning tasks can be mastered in real time. This makes planning activities more transparent while providing information straight to the point.
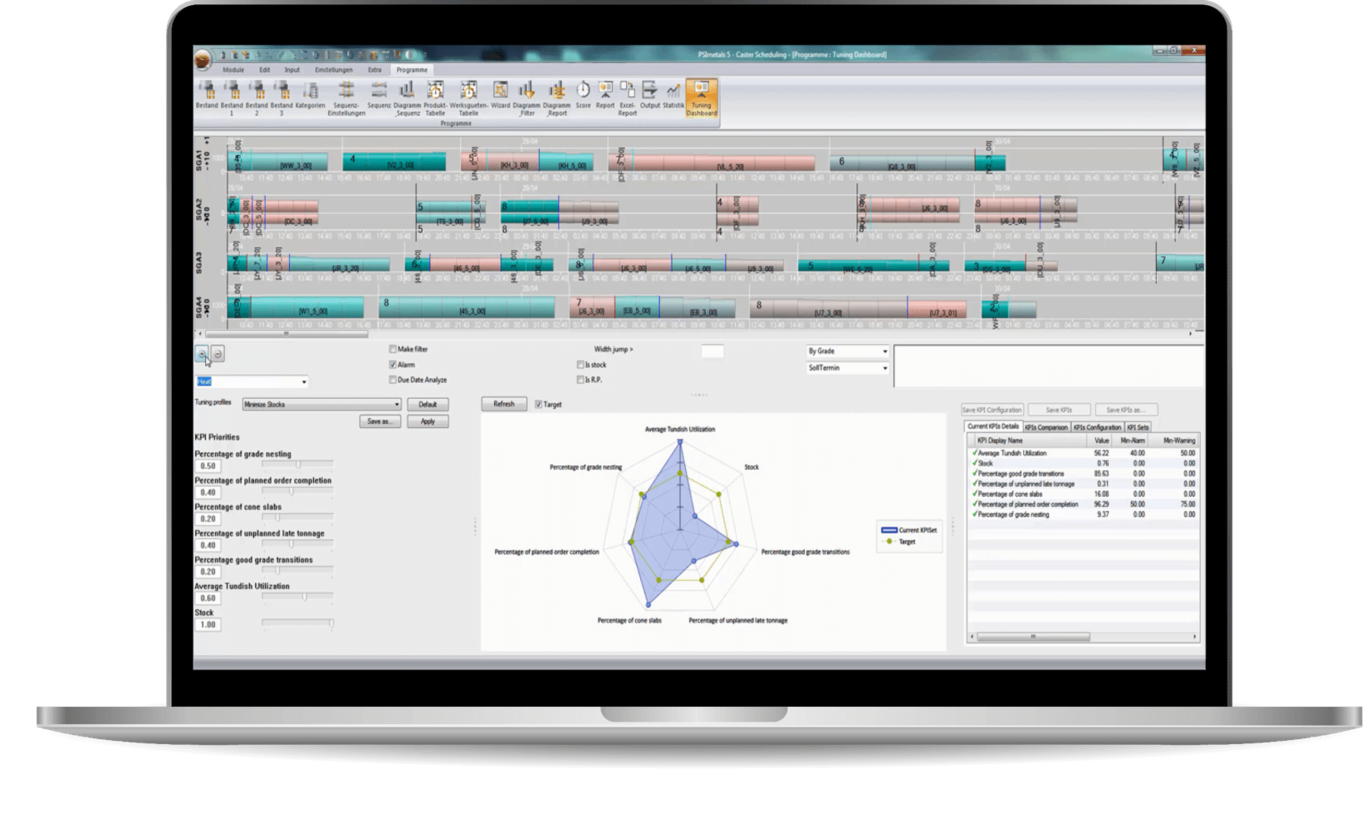
Embedded management of tuning profiles as well as advanced reporting and scenarios benchmarking further support decision makers in finding the best balance between conflicting goals. The access to KPI monitoring can be adapted to each organizational level of the plant down to the shop floor. Experience has shown that feedback information such as KPIs can significantly increase the motivation of production teams.
Benefits of KPI-driven production planning for steel and aluminum producers
- Reduce throughput times and WIP inventory levels
- Improve product qualities through better respect of scheduling constraints
- Optimize order combinations and maximize through-process yield
- Increase efficiency in the planning processes
- Edit plans and schedules easily
- React fast to plan deviations