Ein Stahlwerk zu betreiben bedeutet, eine Vielzahl von Wechselwirkungen zwischen vielen verschiedenen Optionen zu verwalten. Hunderte von Entscheidungen, die auf Produktionsdaten, Berichten und Leistungsindikatoren (KPIs) basieren, müssen täglich von verschiedenen Beteiligten getroffen werden. Der Produktionsplanungsexperte Robert Jäger stellt einen praktischen Ansatz und ein unterstützendes Werkzeug für Planer vor, das bei diesen Aufgaben hilft.
TechTalks über KPI-gesteuerte Produktionsplanung
Produktionsplanung für Stahl und Aluminium: 3 Schritte zu einem erfolgreichen Produktionsplan
Um einen optimalen Produktionsplan zu erstellen, müssen Stahlproduzenten grundsätzlich den 3-Schritte-Ansatz anwenden:
- Schritt 1: Definition von Unternehmenszielen
- Schritt 2: Beschreibung der Strategie und Positionierung
- Schritt 3: Agil sein!
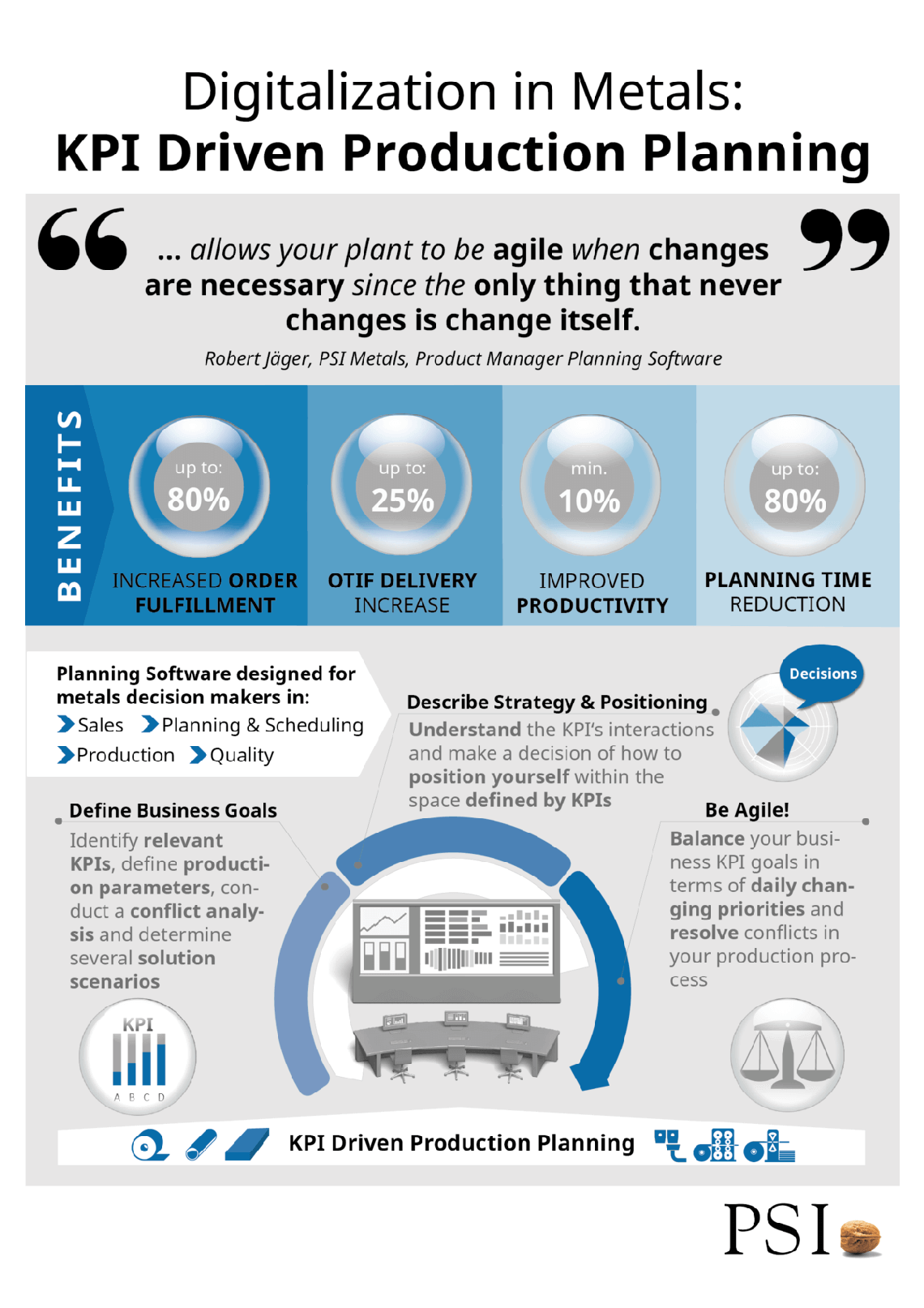
Schritt 1: Definition von Unternehmenszielen
Die Definition von Unternehmenszielen ist der erste und wahrscheinlich wichtigste Schritt auf dem Weg zu einem optimalen Produktionsplan. In einem Stahlunternehmen werden die gemeinsamen Unternehmensziele in der Regel in die Leistungskennzahlen (so genannte Key Performance Indicators, KPIs) übersetzt, an denen die Qualität der Produktionspläne gemessen wird. Dazu gehören die termingerechte Lieferung, die Kapazitätsauslastung sowie die Bestandsmanagement.
Folglich muss jedes Werk die für seine spezifischen Lieferkettenbedingungen relevanten KPIs ermitteln und die Formel für deren Messung genau festlegen. Durch die Definition dieser Produktionsparameter können Ziele für die Bewertung der KPI-Qualität festgelegt werden.
Schritt 2: Beschreibung der Strategie und Positionierung
Während einige KPIs Hand in Hand gehen, gehen andere in entgegengesetzte Richtungen und stehen daher in Konflikt zueinander. Der zweite Schritt besteht also darin, zu verstehen, wie diese KPIs miteinander interagieren, und eine Entscheidung darüber zu treffen, wie man sich in dem durch diese KPIs definierten Raum strategisch positioniert.
Schritt 3: Agil sein!
Nichts ist so beständig wie der Wandl und irgendwann wird man mit neuen Bedingungen konfrontiert sein, z.B. mit neuen Marktsituationen, neuen Wettbewerbern, usw.. Der dritte Schritt auf dem Weg zu einem optimalen Produktionsplan ist daher Agilität! Wenn Sie mit Veränderungen konfrontiert werden, müssen Sie in der Lage sein, die relativen Prioritäten zwischen Ihren Zielen neu zu bewerten und manchmal sogar die Ziele selbst zu überdenken.
Wie man diesen Produktionsplanungsansatz umsetzt
Zur Umsetzung eines solchen dreistufigen Ansatzes benötigen Sie ein unterstützendes Instrument, das Ihnen hilft, flexibel zu bleibend. Ein solches System hilft Ihnen, KPIs auf benutzerfreundliche Weise zu definieren, zu berechnen und zu analysieren. Darüber hinaus unterstützt es Sie bei der Visualisierung von Wechselwirkungen und Konflikten bestehender KPIs und ermöglicht die Durchführung von Simulationen.
Bei PSI nennen wir diesen Ansatz KPI-getriebene Produktionsplanung. Er ermöglicht die Optimierung von Produktionsplänen auf Basis dynamischer Unternehmensziele, die den gesamten Lebenszyklus vom Vertriebs- und Produktionsauftrag bis zum fertigen Produkt in allen Stufen der Stahl- & Aluminiumproduktion abdecken. Der hohe Automatisierungsgrad mit bewährten Algorithmen sorgt dafür, dass komplexe Planungsaufgaben in Echtzeit bewältigt werden können. Das macht die Planungsaktivitäten transparenter und liefert Informationen auf den Punkt genau.
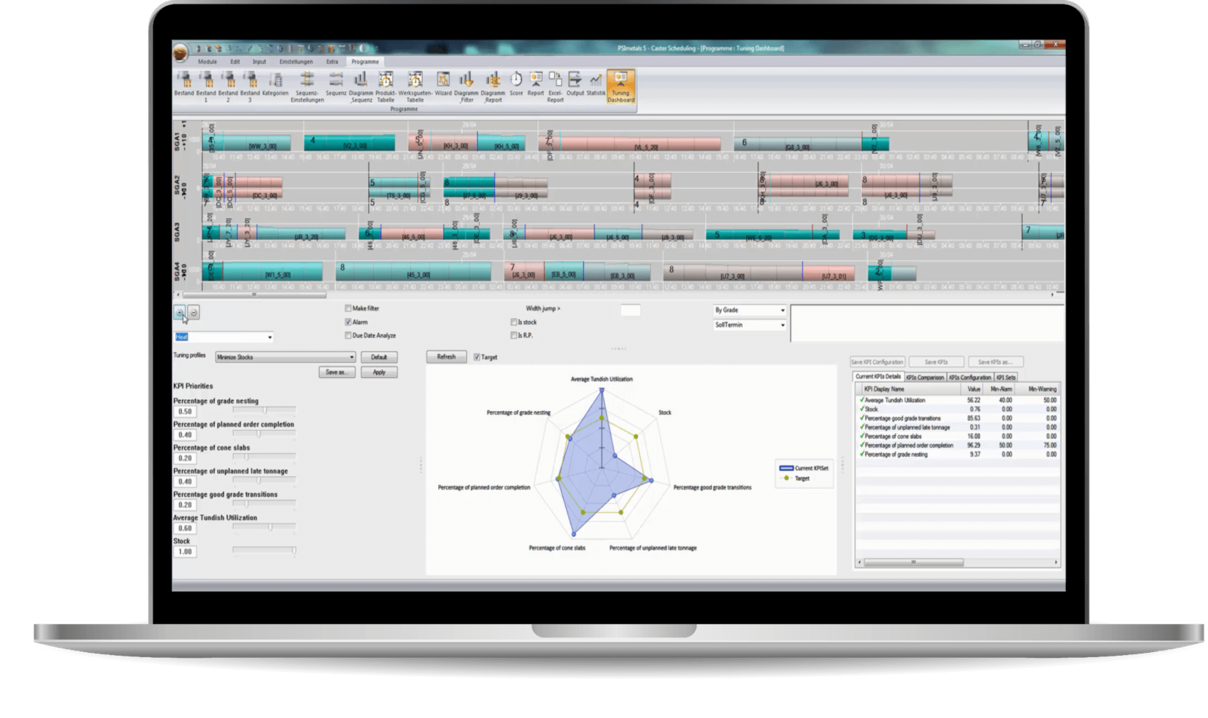
Eingebettetes Management von Tuning-Profilen sowie fortschrittliches Reporting und Szenario-Benchmarking unterstützen die Entscheidungsträger dabei, das beste Gleichgewicht zwischen widerstreitenden Zielen zu finden. Der Zugang zum KPI-Monitoring kann an jede Organisationsebene des Werks bis hin zum Shopfloor angepasst werden. Die Erfahrung hat gezeigt, dass Feedback-Informationen wie KPIs die Motivation der Produktionsteams erheblich steigern können.
Vorteile einer KPI-gesteuerten Produktionsplanung für Stahl- und Aluminiumproduzenten
- Verringerung der Durchlaufzeiten und der Umlaufbestände
- Verbesserung der Produktqualität durch bessere Einhaltung der Planungsvorgaben
- Optimierung von Auftragskombinationen und Maximierung des Durchsatzes
- Steigerung der Effizienz in den Planungsprozessen
- Einfache Bearbeitung von Produktionsplänen
- Schnelles Reagieren auf Planabweichungen