In contrast to larger transport operators, companies with smaller fleets usually only employ a few people to deal with digital issues instead of employing an entire IT team. Until now, a lack of resources was considered a decisive criterion against many digitalisation projects, especially since everyday operations could be ensured without the corresponding systems. In addition, the companies feared that they would become dependent and lose their existential flexibility advantage over larger transport companies.
Resource scarcity was previously seen as a decisive criterion against many digitalisation projects, especially as day-to-day operations could be ensured without the corresponding systems. In addition, companies feared that they would become dependent and lose their existential flexibility advantage over larger transport companies.
Digitalisation as a competitive factor
This has changed with the "zero emission" strategy in public transport and the ongoing electrification of bus fleets. This is because charging management, range and circulation calculations and the dual operation of diesel and electric buses create a complex planning reality that can only be mastered with software support. At the same time, it can be assumed that proof of corresponding systems will increasingly be required when awarding route licences and will therefore become a competitive factor.
As a result, the pressure to act has also increased massively for smaller companies in a short space of time. This has led to the realisation that the introduction of a depot management system is indispensable.
Customizable turnkey complete solution
Smaller transport companies need a system that enables them to ensure the availability and punctuality of their vehicles in the same way as large companies. And which is designed in such a way that even a small number of employees are able to carry out the implementation project successfully.
The PSIeDMS start depot management system from PSI Transcom fulfils this practical requirement. The system is designed as a turnkey solution. It is robust, also suitable for fewer vehicles and can be expanded step by step.
The basic system consists of the 4 modules
- Visualisation,
- supply,
- scheduling and
- and parking
This provides companies with all the necessary functionalities to efficiently manage vehicles of all drive types. The connection to a charging management system for electric buses, to upstream timetable systems (VDV publication 452) and the option of importing master data and generating reports are also included.
In addition, the solution is introduced in line with a defined standard process, which the companies implement largely independently. The order in which the modules are introduced can be customised to the needs of the companies.
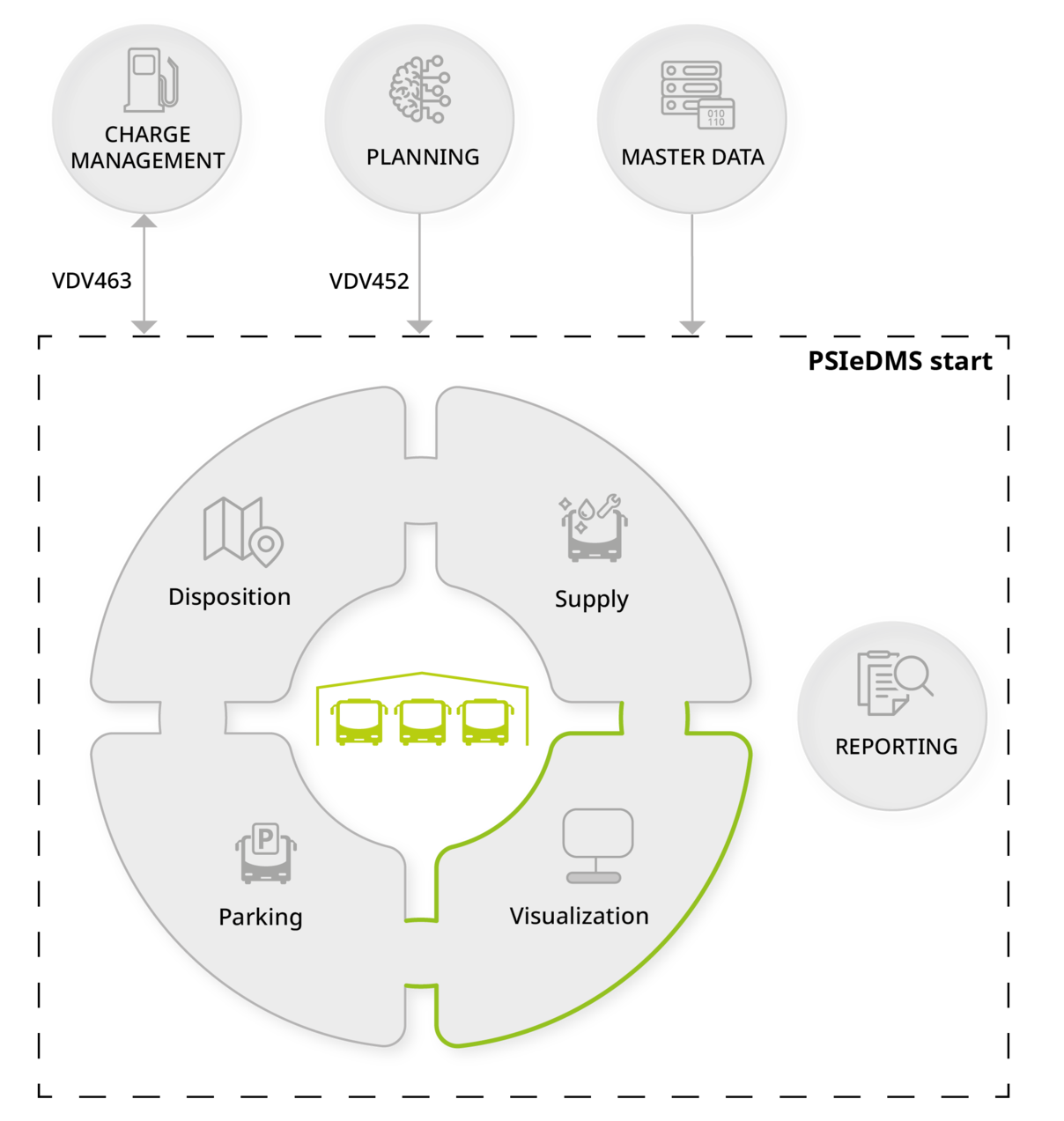
From digital core processes to autonomous systems
When transport companies introduce a basic system, they can limit themselves to digitising the core processes of their depot without taking any functional risks.
With the basic system, they create a digital foundation that provides access to all the latest enhancements. If requirements increase, upgrades can be used to integrate additional modules and automate processes. These expansion packages can also be introduced gradually and therefore with significantly reduced complexity.
The final expansion stage corresponds to the highest level of automation: the system can be operated completely autonomously:
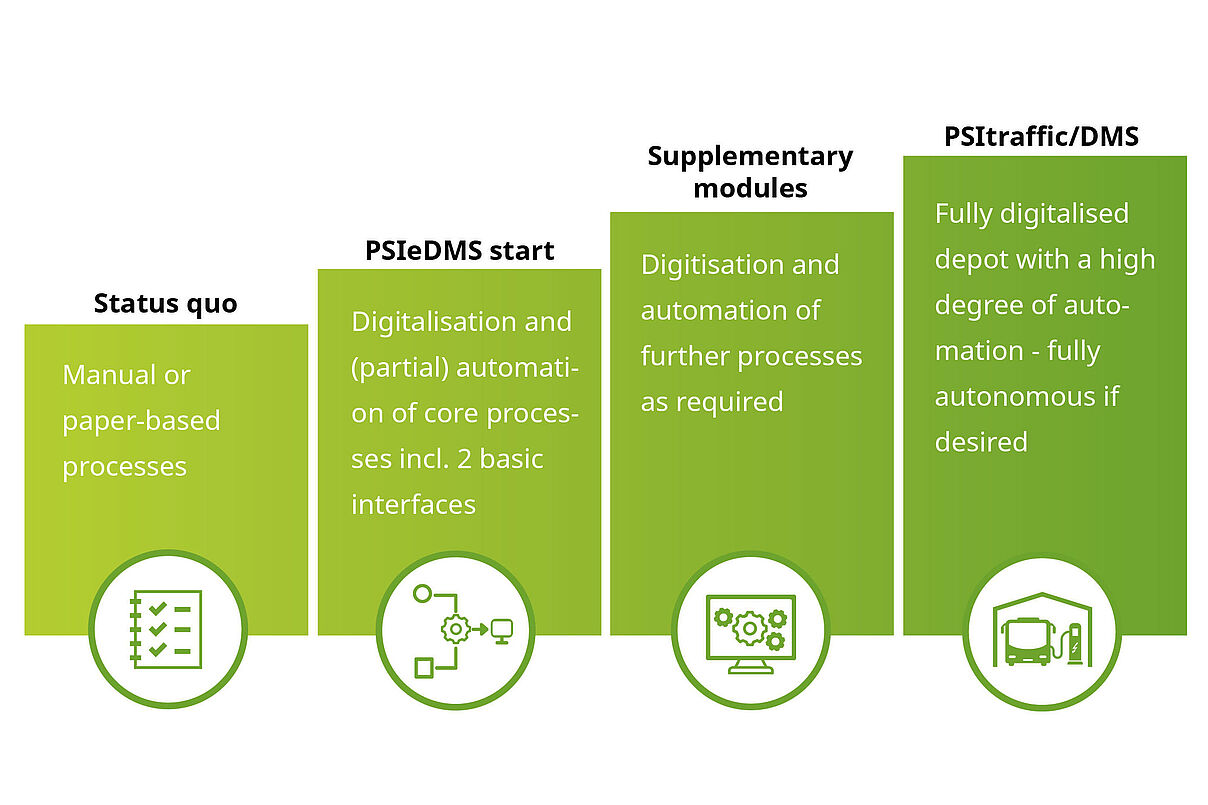
One system for all company sizes
With the electrification of drives, the digitalisation of depots is unavoidable for operators. The introduction of a depot management system opens up the path to digitalisation for modern companies:
With a fixed range of functions and along standardised processes, projects with low complexity are implemented quickly and reliably, while at the same time creating the basis for expansions in line with requirements.