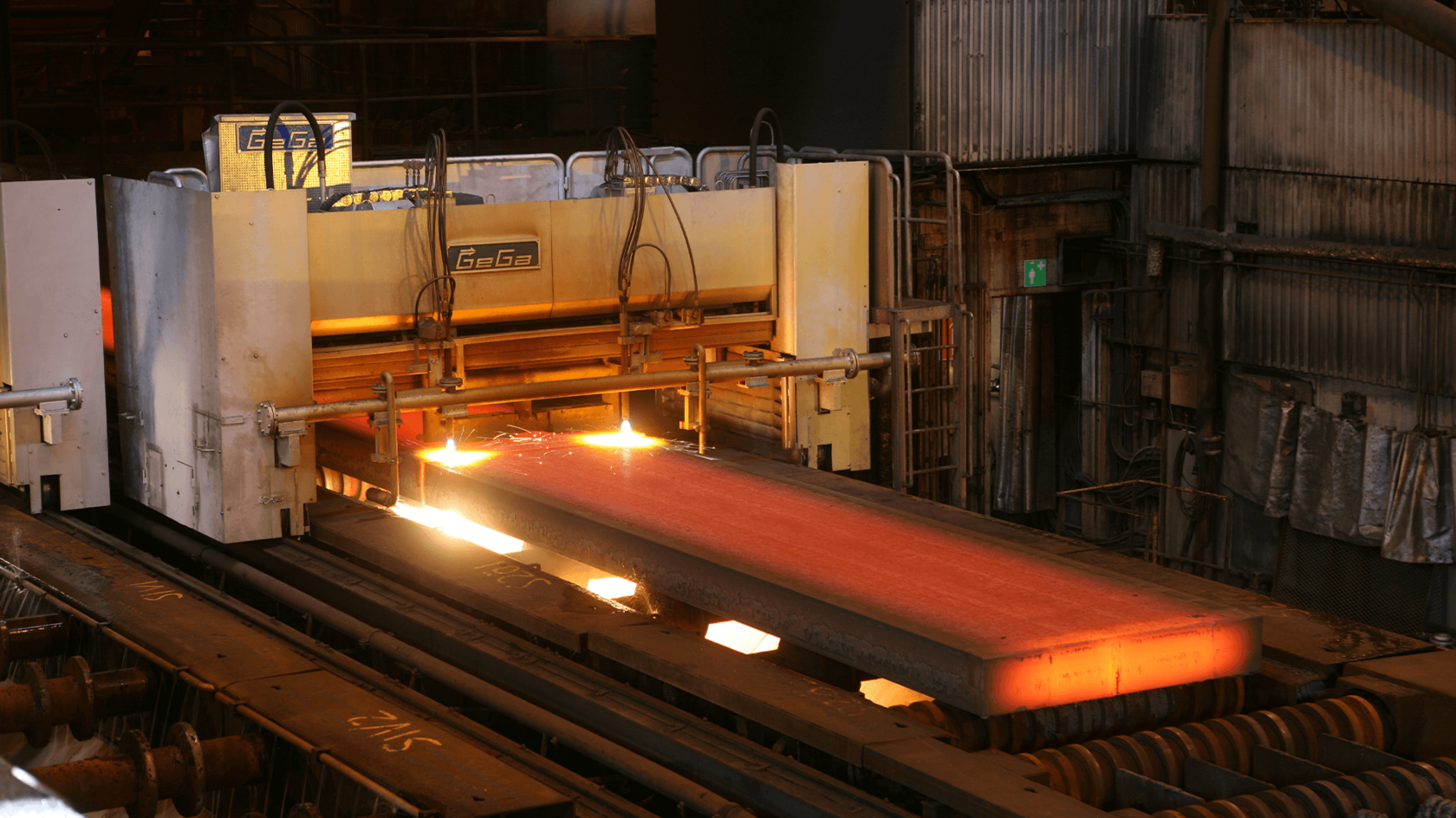
Case Study PSImetals at SSAB Mobile, USA
Holistic visibility of plant-wide scheduling.
SSAB is a Nordic and US-based steel company that builds a stronger, lighter and more sustainable world through value added steel products and services.
Interesting facts about SSAB
The company is the largest producer and supplier of carbon plate in North America, with a market share of approximately 30% in 2023.
The SSAB Mobile facility in Axis, Alabama, is a steel mini-mill which includes an electric Arc Furnace, Ladle Metallurgical Furnace, vacuum degasser, continuous slab caster, and a combination rolling mill capable of producing plate and hot rolled coil. The downstream lines include two quench and temper lines, a normalizing line, and a blast and paint line.
Challenges
- SSAB installed a new quench and temper production line, which was expected to significantly increase the complexity of the production flow.
- SSAB Mobile facility was unable to provide production planning department with a plant-wide visibility in the Production Planning and line planning.
- SSAB was unable to balance their line capacities, and create detailed line schedules considering the special requirements of each individual production line.
- The facility was unable to automatically adjust material planning based on quality events and other real-time occurrences.
- The facility did not allow users to manually adjust line schedules and slab planning in order to react to production events.
Solution approach
PSI implemented a comprehensive suite of solutions to address these challenges. PSI implemented PSImetals Order Dressing to manage customer orders and prepare them for production, PSImetals Order Scheduler provides a holistic view of all the production lines, PSImetals Line Scheduler allows the user to define parameters and patterns specific to a production line and PSImetals Plate Combiner to manage slabs and optimize them for slab size.
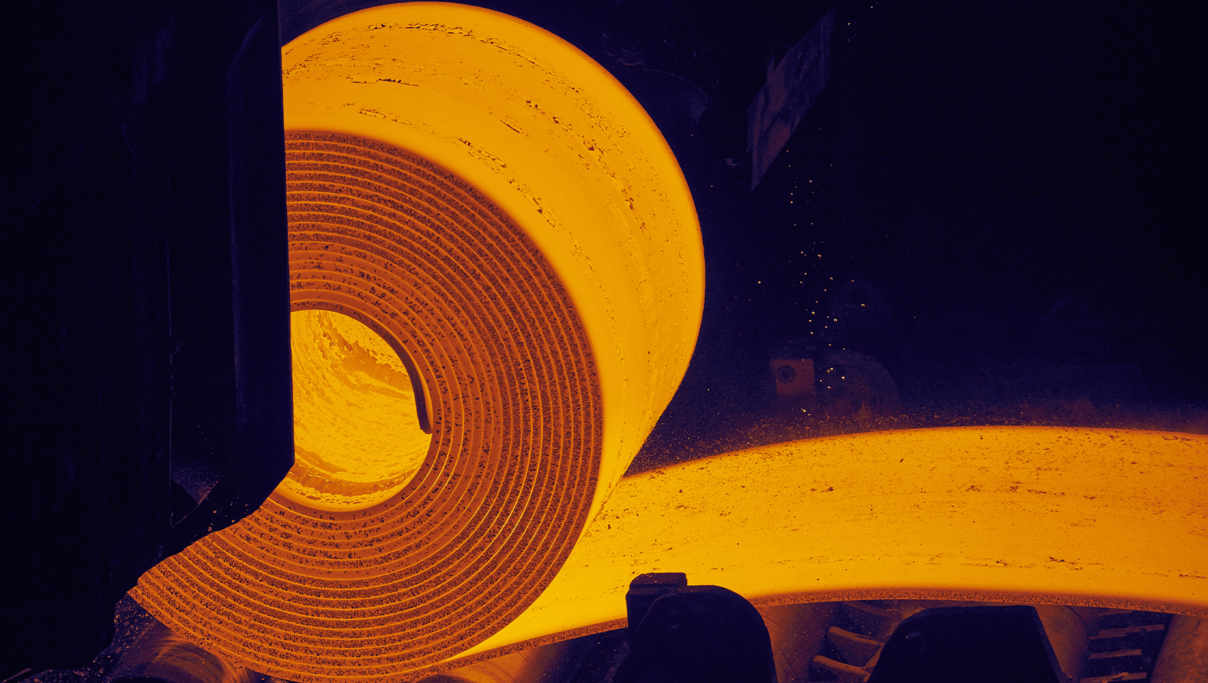
The results
- PSImetals improved visibility and control of the production, enabling better planning and execution.
- Minimized disruptions and ensured smooth production flows through real-time monitoring and adjustments.
- Enabled quick adjustments based on data, improving responsiveness to production events.
- Positive feedback from users on the system's ease of use and effectiveness, with improved capabilities for adjustments.