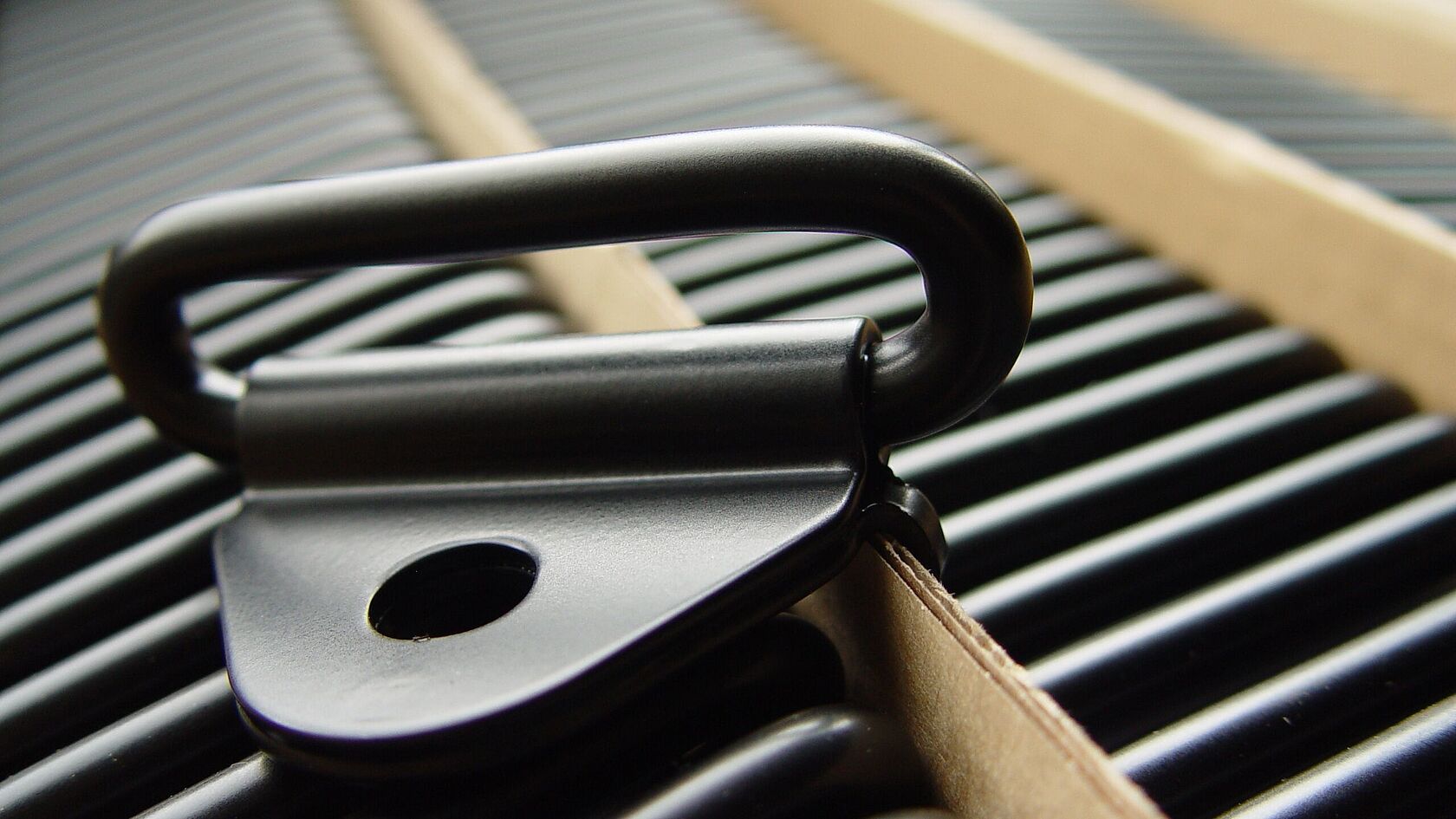
Case Study Lenzkämper optimizes planning and production processes with PSIpenta/ERP
The automotive supplier meets demanding OEM requirements, e.g. in the areas of packaging structures and traceability.
As an automotive supplier, Lenzkämper has to overcome a variety of challenges. Above all, it has to meet the increasing requirements of OEMs and optimize its own planning and production processes accordingly. This includes, for example, connecting to OEM portals, mobile applications, end-to-end batch traceability and mapping the required packaging structures. The wire forming technology specialist relies on the PSIpenta ERP system, which is specialized for the industry.
About Lenz, Kämper GmbH & Co. KG
Lenz, Kämper GmbH & Co. KG - Lenzkämper for short - is one of the classic automotive suppliers that supply manufacturers such as Volkswagen, Seat, Skoda, Audi and BMW worldwide. The core business of the medium-sized company is bent wire parts, such as belt deflection fittings, brake cable holders or lashing eyes. However, Lenzkämper's service portfolio also includes technical advice and the production of complex welded assemblies and hybrid components. The ready-to-install components are supplied to OEMs as well as to companies in other industrial sectors.
Challenges
Like all suppliers, Lenzkämper is particularly bound by the restrictions and regulations of the OEMs. As a result, the importance of information technology - above all the ERP system - has gradually grown over the company's 90-year history. The old ERP solution had reached its limits in many respects and could no longer meet the growing demands of customers, e.g. in terms of data exchange and certifications as well as the required flexibility, scalability and openness.
Stringent OEM specifications
In addition to the creation of manufacturer call-offs and the consideration of VDA standards, the creation and management of the complex and at the same time very different packaging structures required by the car manufacturers is challenging. Among other things, they specify how many parts must be packed in which containers, how many levels a pallet may be loaded on, which release agents must be used or whether a lid must be used. The specifications are defined in the framework agreements with the car manufacturers and can vary from customer to customer or from call-off to call-off. In the past, there have been repeated delays and complaints in this regard.
Production features
- Suppliers to the automotive industry
- Stringent specifications from OEMs, including packaging structures
- Outsourcing of special surface treatments
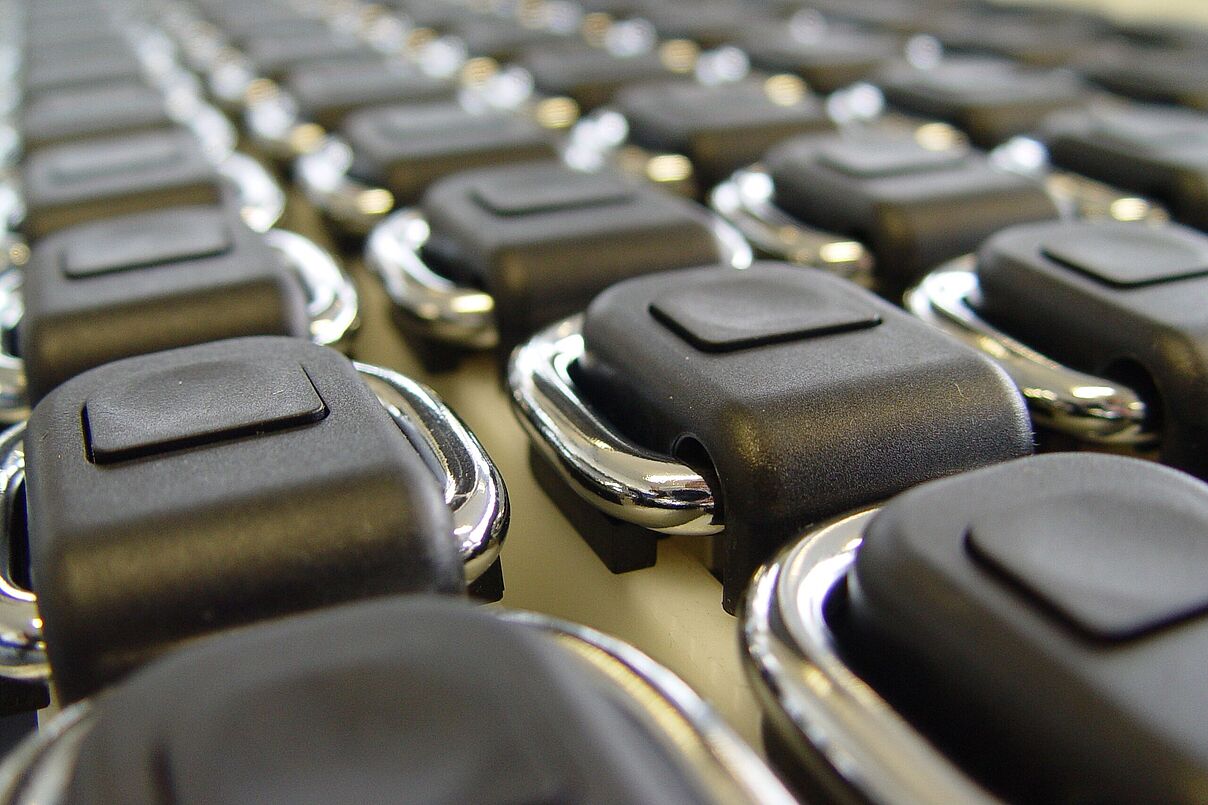
Objectives
Lenzkämper was looking for a new ERP system that would efficiently support the standard processes typical of a supplier in the industry and at the same time offer simple solutions to easily digitize data capture processes in the periphery.
The most important goals
- Improving data collection
- Increasing data quality
- Optimization of (industry-typical) business processes
Solution approach
As an industry solution, PSIpenta/ERP covers numerous typical supplier processes as standard - including the connection to OEM portals, end-to-end batch traceability and the mapping of the OEMs' required packaging structures. More than 50 of the total of 100 employees use the system, which supports the processes of an entire order cycle: from the creation of the OEM call-off via EDI interface, through production, packaging and shipping, to invoicing and the processing of complaints.
Implementation
PSIpenta/ERP uses packaging management to map packaging structures. The system calculates the need for packaging materials based on the production or shipping quantities and triggers corresponding requests. Lenzkämper also uses this module to manage a packaging materials account for each business partnership, in which the entire stock is managed, repackaging processes are controlled and the required traceability of goods down to the individual packaging unit is guaranteed.
Integrated outsourcing also plays a special role, which the company uses, for example, to map the external outsourcing of special surface treatments. When these parts are returned, they are transferred directly to the packaging structure or to shipping in line with customer requirements.
Last but not least, numerous processes have become significantly more efficient thanks to the use of mobile extensions to the ERP system, which run on handheld scanners. They replace many a paper-based document, the one or other manually maintained Excel list or additional paths, e.g. in material removal or for good quantity reports.
The result
Trace parts down to the individual package, process complaints quickly and easily, record data digitally and simply via scanner as well as numerous evaluation options: The list of advantages of the new ERP system highlighted by those responsible is long. They all lead to more efficient processes, replace the error-prone processing of manually maintained documents and save time and effort.
Conclusion
With the ERP standard PSIpenta, Lenzkämper has found a system with which it can meet the functional and technological requirements of its demanding customers in the long term. In addition to the mapping of all required, industry-specific functions, the scalability, openness and therefore investment security of the system are particularly important to the supplier.