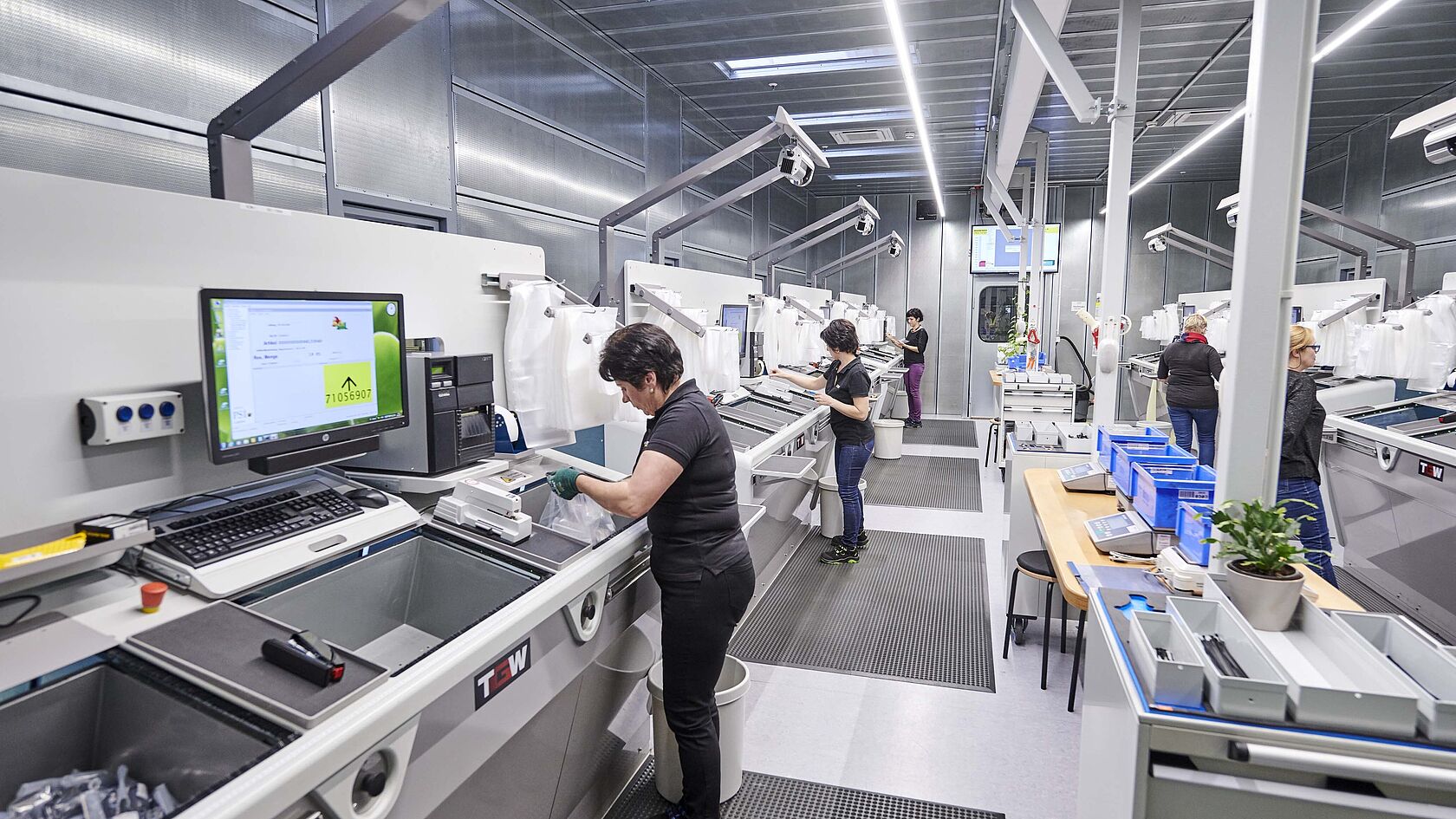
Case Study Increased efficiency with PSIwms at Alfred Kärcher SE & Co. KG
Optimized logistics processes and picking significantly increase performance at the Kärcher central warehouse in Obersontheim.
Alfred Kärcher SE & Co. KG uses the warehouse management system PSIwms in its central logistics center in Obersontheim to optimize storage and picking processes according to product-specific strategies. Since its introduction in 2012, the efficiency of order picking has increased significantly. The modern system solution supports the company in managing a large range of spare parts and accessories and ensures fast and reliable delivery processes for customers worldwide.
Mastering challenges
The central logistics center in Obersontheim houses over 71,000 spare parts and more than 6,000 accessory items. The logistical challenge was to ensure efficient storage and picking processes despite the growing product range and increasing demand. To meet these requirements, Kärcher decided to redesign its internal logistics processes.
Customer's objective
Solution approach
As part of the project, the old high-bay warehouse with 8,000 storage spaces was converted into a replenishment warehouse, while a new fully automated high-bay warehouse with 15,400 pallet storage spaces and an automated small parts warehouse with 85,000 container storage spaces were built. In addition, a block storage area with 6,500 storage locations for picking medium-sized items and a wide-aisle warehouse with 6,200 pallet storage locations for fast-moving items were implemented. A particular highlight is the two-aisle consolidation buffer, which is served by a shuttle system and offers 5,400 container storage locations.
The PSIwms system handles the management and control of the complex storage and order processes. It optimizes inventory management, determines storage areas, calculates routes and transmits work orders to the device controls. Pick-by-voice and pick-by-light technologies are used to improve quality and efficiency. This makes it possible to pick up to 17,000 order items every day, all of which are ready for shipment within two hours. Up to 5,000 packages leave the logistics center every day.
Warehouse characteristics
- 2 high-bay warehouses with 8,000 storage places and 15,400 pallet spaces
- Eight-aisle automatic small parts warehouse with 85,000 container storage locations
- Block warehouse with 6,500 storage locations
- Wide-aisle warehouse with 6,200 pallet spaces
- Order picking system with 130 storage spaces
- Two-aisle, shuttle-operated consolidation buffer with 5,400 container storage locations
The result in detail
The implementation of the new warehouse concept and system solutions has increased picking perfor-mance from 750 order lines per hour to 1,500. The efficiency and reliability of the logistics processes have been significantly improved, resulting in higher customer satisfaction and better competitiveness.
Well-thought-out material flows, state-of-the-art automation systems and an intelligent warehouse management system – with the new logistics center, we wanted to increase our picking performance from 750 order items per hour to 1,500.
PSIwms functions in use
- Cockpit
- Archive
- Event management
- Double-/multi-deep storage
- Dangerous goods
- Hazardous substances
- Weight control
- Handling units management (“TE to TE”)
- Empties and loading aids
- Expiry dates
- Package optimization (case calculation)
- Serial number
- Stacker control system + mobile order processing
Conclusion
By using the warehouse management system PSIwms and modernizing the logistics center, Alfred Kärcher SE & Co. KG has created a powerful and future-proof solution for optimizing its logistics processes. The increased efficiency and improved picking performance enable the company to continue to meet the high demands of the market.