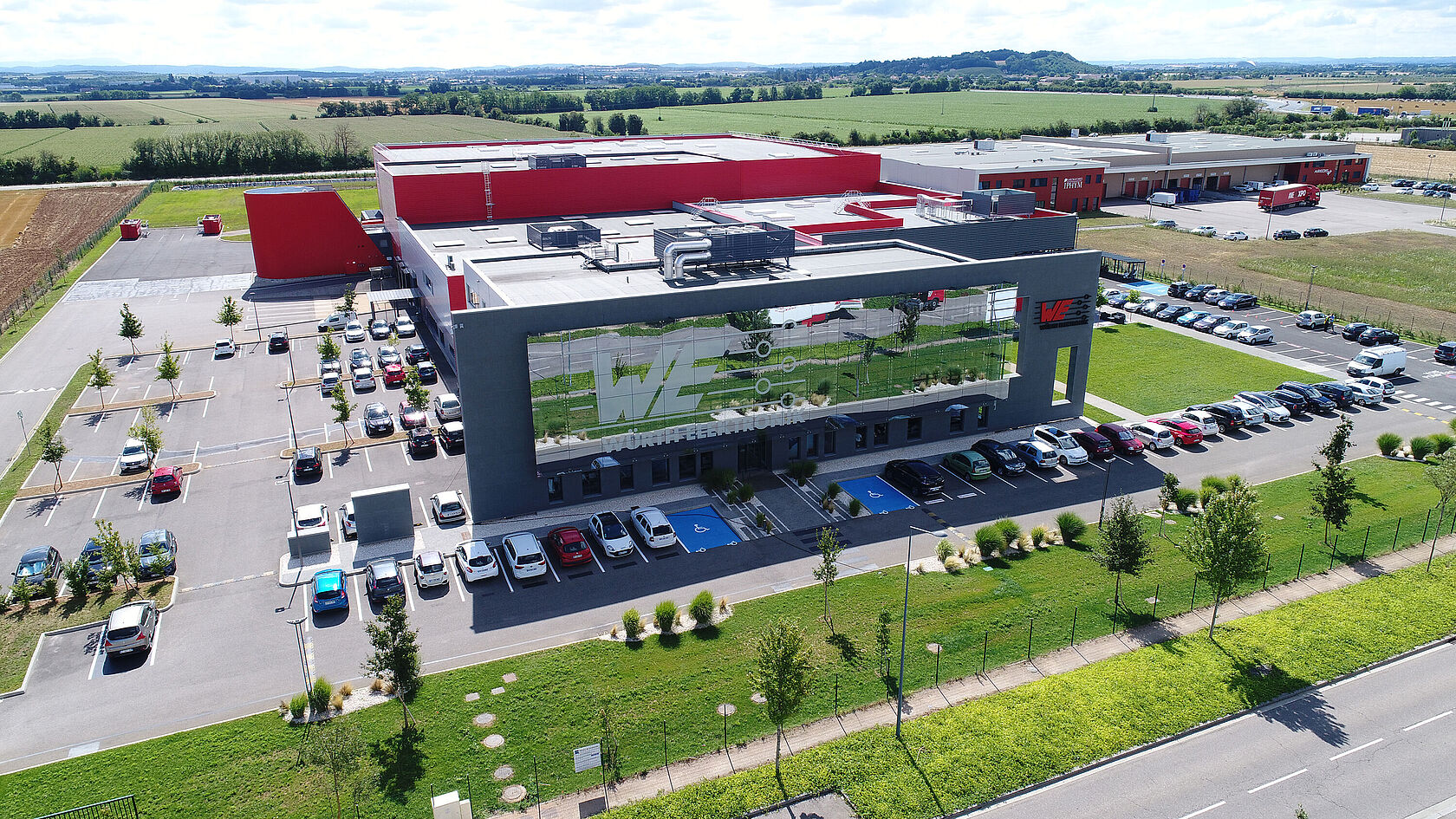
Case Study Efficient logistics automation at Würth Elektronik eiSos
Optimized logistics processes through automation and PSIwms in the central warehouse of Würth El-ektronik eiSos.
Würth Elektronik eiSos GmbH & Co. KG develops and distributes electronic and electromechanical components worldwide. As part of the Würth Group, the company relies on innovative solutions to make its logistics processes efficient and competitive. The PSIwms warehouse management system is used in the central warehouse in Waldenburg and forms the basis for the step-by-step automation of warehouse operations.
Mastering challenges
The central warehouse in Waldenburg holds more than 30,000 passive components for industrial applications that are shipped worldwide. Around 2,000 orders with over 4,500 items are picked every day. Efficient processes are essential here. In view of the increasing demands, Würth Elektronik eiSos planned to implement a fully automated storage system to replace existing manual and scanner-controlled processes. The objectives included the integration of storage location and batch management as well as automated picking according to the first-in-first-out principle.
Customer's objective
Würth Elektronik eiSos's main objective was to fully automate the central warehouse in Waldenburg in order to meet growing efficiency and competitiveness requirements. The seamless integration of storage location management, batch and date code management and picking according to the first-in-first-out principle was to be carried out. The logistics processes were to be designed in such a way that order processing could be carried out faster and more precisely. In addition, the automation was to be implemented step by step during operation in order to minimize disruptions and ensure the continuous functionality of the warehouse.
Solution approach
In order to make the changeover during operation as smooth as possible, Würth Elektronik eiSos relied on the Adaptive Scenario Management of PSIwms. This made it possible to revert to the old configuration at any time in case of problems. The warehouse was equipped with an automatic goods-in recording system and a highly dynamic conveyor system. All incoming goods pass through a measuring tunnel that transmits relevant data such as weight and dimensions to the PSIwms material flow computer. The goods are efficiently processed at twenty picking stations using pick-by-light and pick-to-light systems. In addition, special packing stations have been set up that are optimally controlled by PSIwms. Orders that correspond exactly to the stored packaging units are routed directly to the dispatch line via a by-pass in order to relieve the picking and packing stations.
Warehouse characteristics
- 11,180 sqm of storage area
- up to 200,000 storage positions
- 9 aisles shuttle warehouse with 38 levels
- 99 level-changing shuttles, 2 double gondola lifts
- 12 CEP goods receipt stations
- 20 fully automated order picking stations; incl. special order picking stations for ESD articles (electrostatic discharge)
- 16 packing stations
- Control of 27 dispatch lanes depending on the shipping mode
- Special storage for moisture sensitive articles (different temperature zones)
- Re-reeling (in conjunction with rolled goods)
- Automatic goods receipt via measuring tunnel (2D barcodes)
The result in detail
By implementing PSIwms and gradually automating the warehouse processes, Würth Elektronik eiSos has been able to significantly optimize its logistics processes. Automated picking and the integration of storage location management have led to a significant increase in efficiency. The company is now able to process orders faster and more accurately, while the flexibility and adaptability of the system allows for future expansions.
With PSIwms, order processing is fast and efficient. Thanks to its update and release capability, we are also well prepared for the future.
PSIwms functions in use
- Pick-by-light, automatic test, batch management
- Multi-level packaging units, value-added services
- Adaptive scenario management, archive
- Multi-storage capability (interaction between locations in Waldenburg, Germany und Lyon, France)