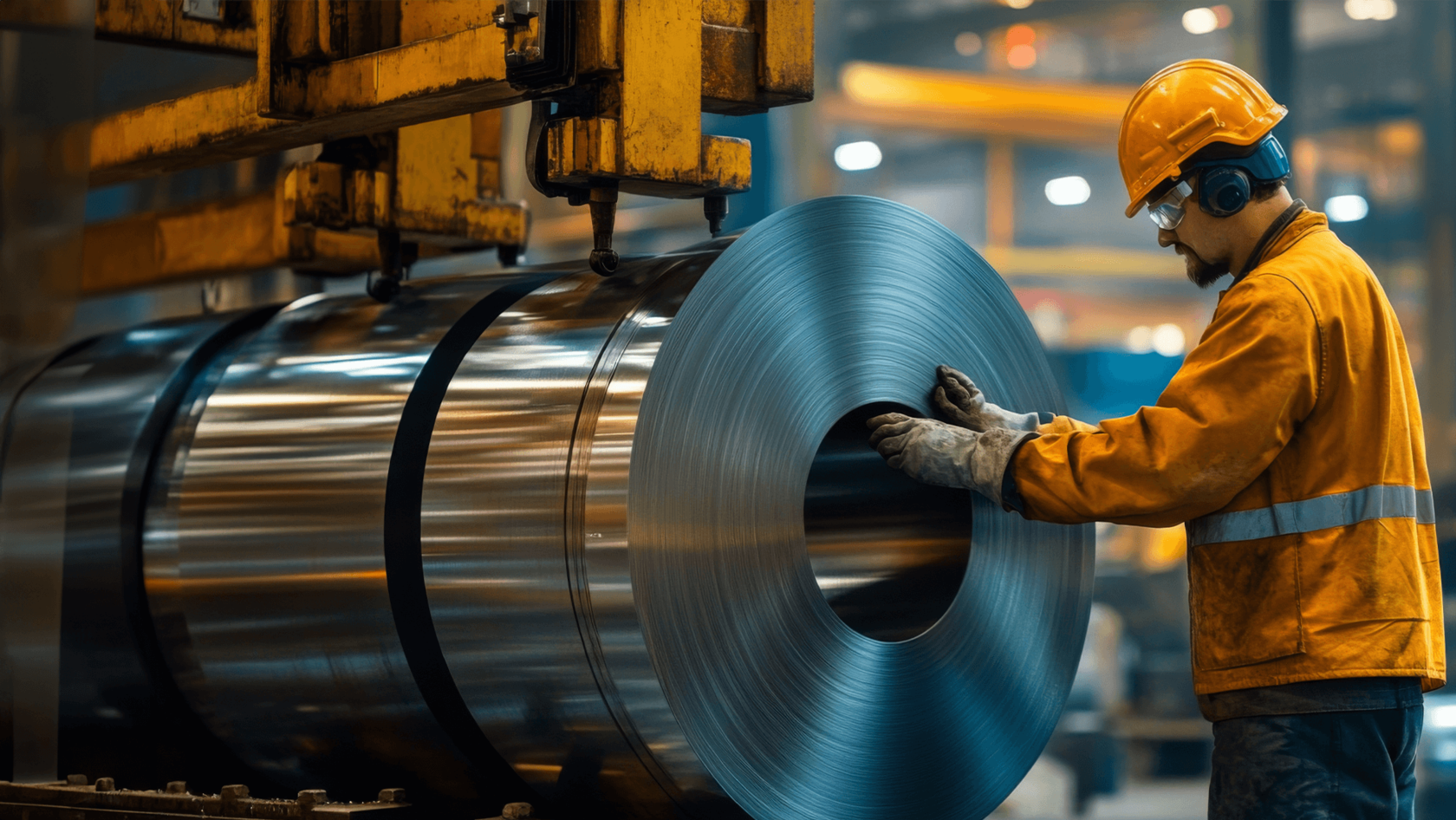
International steel and aluminum standards typically require quality control at the finished product stage. Identifying quality issues at this stage could result in being removed from the order. Being forced to downgrade a finished product and deallocate it from the original order is the worst-case outcome: it results in delivery delays, difficulty in reassigning the product to another order, or even complete material waste, leading to high financial loss. Detecting (or predicting) quality issues early in the production route enables more effective responses and significantly reduces the risk of forced deallocation.
Challenges
In the metals industry, round-the-clock manufacturing generates large volumes of highly diverse materials and data, making comprehensive manual assessment and control impossible. At the same time, knowledge gaps among plant managers could impact effective quality control. Furthermore, executing unplanned corrective operations in a complex environment that is typical of the metals industry requires flawless coordination, which cannot be attained via telephone, email, manual intervention alone.
Make the right data available
In a metals manufacturing plant, collecting process data and making it available for an end-to-end production overview is challenging. To extract value from this large volume of data, the ability to trace material genealogy and accurately display and correlate process data across various production steps is a prerequisite.
Translate knowledge into quality control
Product and process knowledge typically resides in R&D and Quality Departments, but is often only utilized at specific points—during product design or when material failures are identified in final quality control. Systematic monitoring of in-progress materials using metallurgical expertise is ideal, but impractical to implement manually. Level 2 automation systems cannot fully support this task because their focus is to control individual process parameters of a single production line, rather than their interactions and impact on the final product. How can this gap be addressed?
Execute precise reactive measures
When quality issues are identified, material-specific compensation measures may sometimes be implemented, deviating from the predefined manufacturing instructions outlined in the Production Order. However, executing such unplanned actions in the complex environment of the metals industry is challenging. Multiple processes, including scheduling, production preparation, and logistics, must be adjusted, and new information needs to be communicated across various locations without disrupting regular production. This cannot be managed through informal communication like e-mails, phone calls, etc. among employees. To ensure success, these adjustments must be fully and seamlessly supported by the Manufacturing Execution System (MES).
Systematic and knowledge-based online evaluations of process data at any production step minimize risks and enable prompt, informed responses.
PSImetals Quality offers a robust framework for translating product and process knowledge into systematic quality control. With Process Value Archiving Management (PAM), digital data for any work-in-progress material can be collected from Level 1 or Level 2 automation systems and measurement devices. This data is visualized in configurable charts and centrally accessible across the plant.
PSImetals Process Quality Decisions (PQD) allow quality checks at any production step, evaluating Quality Indicators against targets to identify risky materials early. These materials can be blocked and flagged for Nonconformity management, enabling users to take corrective actions or initiate dedicated Production Orders for individual critical materials, ensuring the effective scheduling and execution of rework operations or parameter optimization.

Usage scenarios
Scenario 1: Preventing failure due to minor surface quality
Frequently, surface defects appear only after rolling but stem from issues in the casting process. PSImetals collects relevant process data from the melt shop and caster, mapping it to each cast slab to calculate significant Quality Indicators. PSImetals PQD compares these indicators with targets based on surface quality requirements from the Production Order.
Violations generate a Nonconformity that blocks the slab(s). The quality engineer can then deallocate the risky slab or create a Rework Production Order for scarfing prior to hot rolling.
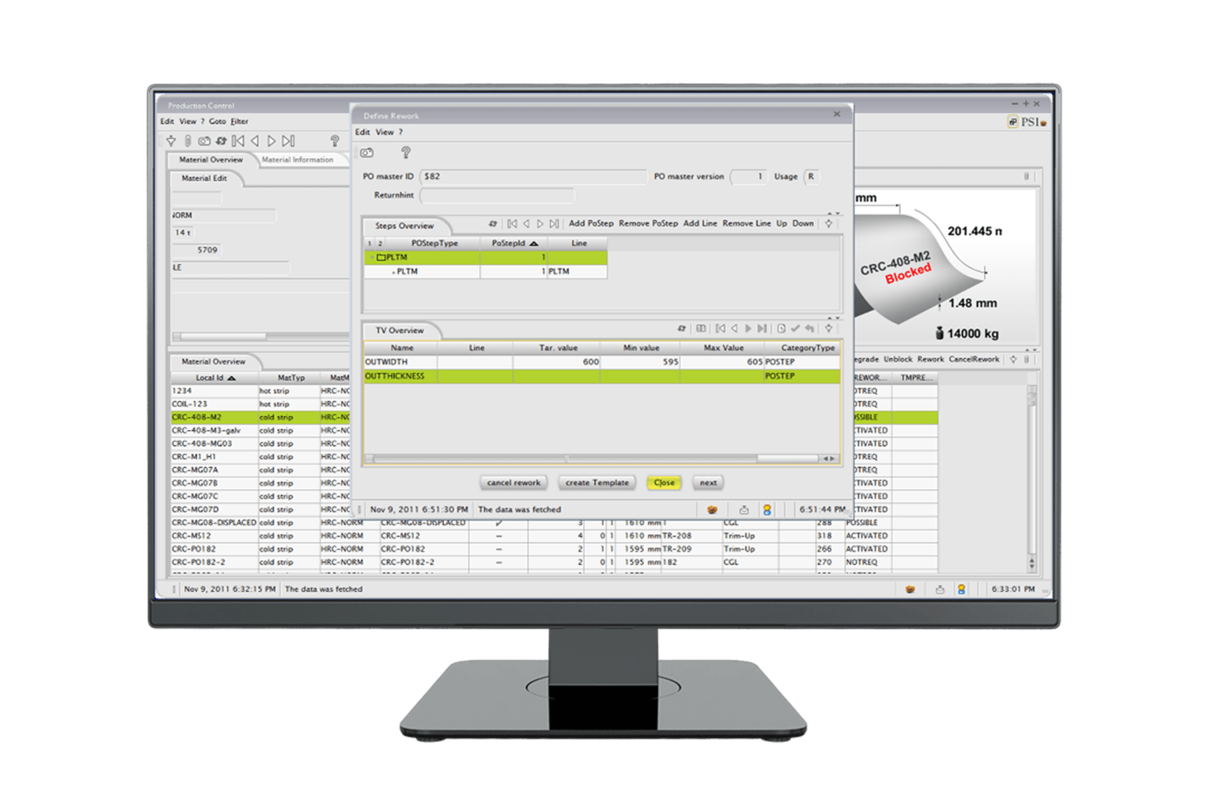
Scenario 2: Preventing failure due to insufficient mechanical properties
Mechanical properties arise from the interplay of various process parameters along the production route. While controlling each parameter within industrial tolerances is useful, it cannot eliminate the risk of unfavorable combinations.
Quality Indicators enable the assessment of a hot-rolled coil—used as input for a galvanized cold-rolled coil—by combining its chemical composition and hot-rolling parameters.
If PSImetals PQD evaluates the Quality Indicator(s) negatively, after hot rolling, a Nonconformity Code is assigned to the hot rolled coil, triggering a Forward Dressing request. This generates a Material Production Order with compensatory measures, such as assigning a higher annealing temperature in order to mitigate the risk of excessive strength in the final product. The dedicated Material Production Order also ensures appropriate scheduling and logistics.
Benefits
-
Address quality issues proactively at the earliest stage possible
PSImetals PQD reduces time and material loss while enabling prompt responses.
-
Translate knowledge into action
Quality Indicators transform in-house knowledge into key metrics extracted from collected process data, enabling their use for online quality control.
-
Seamless nonconformity management
Corrective measures are provided to the MES in the form of material-specific Production Orders, ensuring smooth scheduling and execution.
Conclusion
Beyond managing the quality control of finished products (tests and inspections), PSImetals enables the use of process data for quality control of work-in-progress materials. Through configurable rules and functions, in-house expertise on product and process can be systematically applied after each production step to detect quality issues early and implement corrective measures. These Advanced Quality services help improve First-Time Right and On-Time, In-Full Delivery performance, ensuring higher production efficiency and reducing defects.