When you listen to steel and aluminum production, often all you hear is deafening noise as customer satisfaction drops and production costs rise due to missed quality expectations. With digitalization, producers can finally take a deep breath and enjoy the silence of a smooth shopfloor.
When people think about a product, the first thing that immediately comes to their minds is the price. But if you ask them what they think about the quality of the product, they would answer that they find quality in general very important and (especially for the price) somehow self-evident. Indeed, quality only stands out if it doesn’t meet expectations and requirements – bad quality creates noise. At the same time, it’s a strong cost driver which makes quality a costly and sometimes annoyingly noisy implicitness.
Fading out steel quality noise with big data
Fading out production noise and offering the best quality goods by collecting mass data can be highly effective. Big data is just like sound-cancelling headphones in a loud environment.
Over 500,000 measurements are recorded by sensors just for rolling one coil, accounting for a wealth of data that one person cannot mine. However, the purpose of collecting production data is, just like silence, often misinterpreted. The key to a smooth production is not the mass data themselves, but the ability to assign meaning to them in their individual process context and to reconcile them with all actors in current and past production.
You need to identify and understand quality issues, track them back to their origin and finally learn how to mitigate them in the future. This approach is neither rocket science nor new, but the availability of new tools and technologies around Industry 4.0 and digitization makes it worthwhile - again.
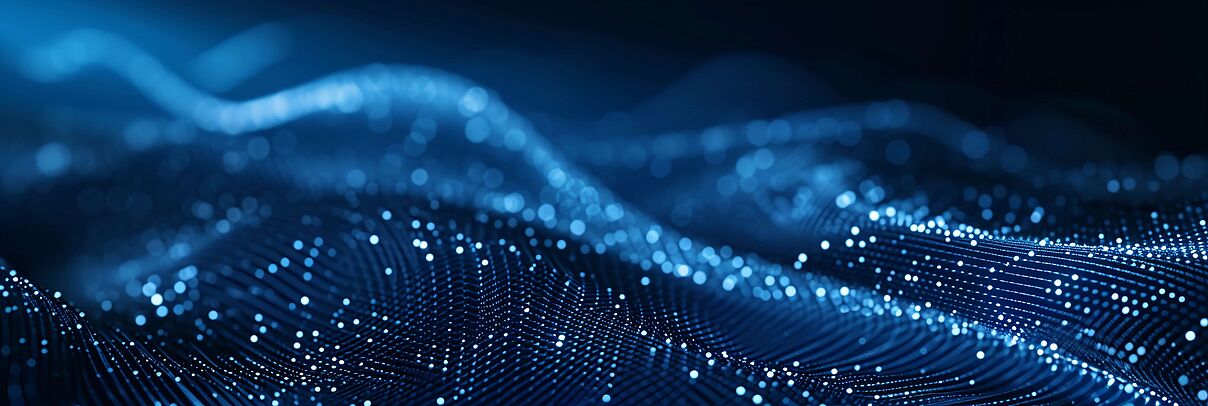
Seeing the big picture in steel quality
If it’s not new, what’s the game changer then?
With this holistic approach we’re able to replace previous system silos for data analysis. The integrated view and contextualized data relieves users from the tedious task of making the information that was obtained from the system silos comparable. Instead, users have faster and easier access – leaving more time for improving the quality through the added value of the information obtained.
Holistic silence – Discover the sound of advanced quality management in steel production
With PSImetals Quality we’re now throwing the door wide open to the world of mass data processing, Machine Learning and thus the idea of a closed quality control cycle. By combining time-critical, process-based data with material-related measurements values throughout the entire material genealogy, the concept of Quality Indicators (QI) makes the holistic approach a respectable possibility. Following the concept, the system is able to make a quality decision based on complex data situation immediately after a production process, far richer than a simple comparison of material data to target order requirements, and without the need for lengthy sampling processes.
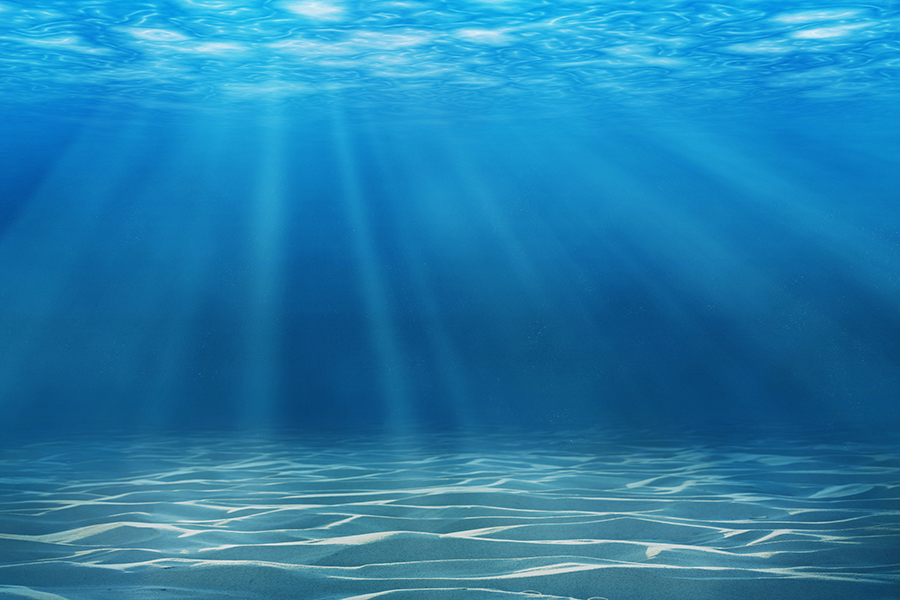
Autonomous steel quality decisions for smooth shopfloor
The concept of QIs opens up entirely new horizons. Together with PSI’s Deep Qualicision framework, autonomous quality decisions become reality! In addition to the final product quality, the stability and reliability of the process are also a fundamental key to success. The Factory Model, the Digital Twin of the production environment, contains the genealogy of all materials together with all process-related data. Together with the QIs, the Factory Model forms the perfect basis for quality forecasts. Precisely with highly integrated, time-critical processes such as heating, detecting quality issues in the process can ensure that the material flow is maintained and secure the associated customer satisfaction – a “Mission Impossible” for system silos. Industrial Intelligence at its best!