Implementing such systems has long been a challenge, but Hisert's e-commerce warehouse has seen a remarkable increase in efficiency through the integration of a preconfigured WMS.
Hisert, a manufacturer and distributor of apparel, footwear and accessories via e-commerce platforms, commissioned a new warehouse in Szczecin in mid-2022. Covering an area of 11,500 square meters, the warehouse handles the shipment of several thousand garments and accessories per week. 100% of the volume shipped from the new warehouse is sent to customers of marketplace platforms such as Zalando, eBay and Amazon. The investment is expected to strengthen Hisert's competitiveness. The opening of the new warehouse provided an opportunity to fully digitize the company's logistics processes.
Seamless transition from legacy system to proven PSIwms
Initially, the logistics processes in the new warehouse were handled using the old WMS system. However, the rapid increase in orders presented a challenge, which is why Hisert decided to switch to the proven PSIwms.
When choosing a WMS system provider for our first distribution center, we focused on several key criteria. We were looking for a system with proven use in e-commerce distribution, especially in the fashion industry. A rapid implementation was also a high priority. In addition, the system should allow for future business expansion.
PSI Polska's track record includes WMS system implementations in warehouses of CCC, Half Price or LPP - owners of Reserved, House, Cropp, Mohito and Sinsay brands, to name a few.
Advantages of a preconfigured system
Hisert deliberately chose the preconfigured version of PSIwms, which is tailored exactly to the requirements of an omnichannel system. This model is based on experience from other successful implementation projects. By working with PSI Polska, Hisert was able to draw on proven solutions and adapt them to the company's specific requirements. This approach significantly accelerated the system implementation and minimized the risk of errors and delays.
"At every stage of the project, including the launch, we could fully rely on PSI's professional and comprehensive support.
This support proved crucial, especially because when we opened our first distribution center, we had not yet specified all logistics processes down to the smallest detail - a situation that would have presented challenges for many WMS providers. But thanks to PSI's preconfigured system, we were able to rely on proven solutions.
Our approach was to take existing processes and adapt them precisely to our business requirements. This significantly accelerated the system implementation and minimized the risk of potential project problems.
In projects of this kind, it is essential to form a true partnership with the system provider in order to benefit optimally from their experience and expertise," explains Wojciech Drobczyński, Process Manager at Hisert.
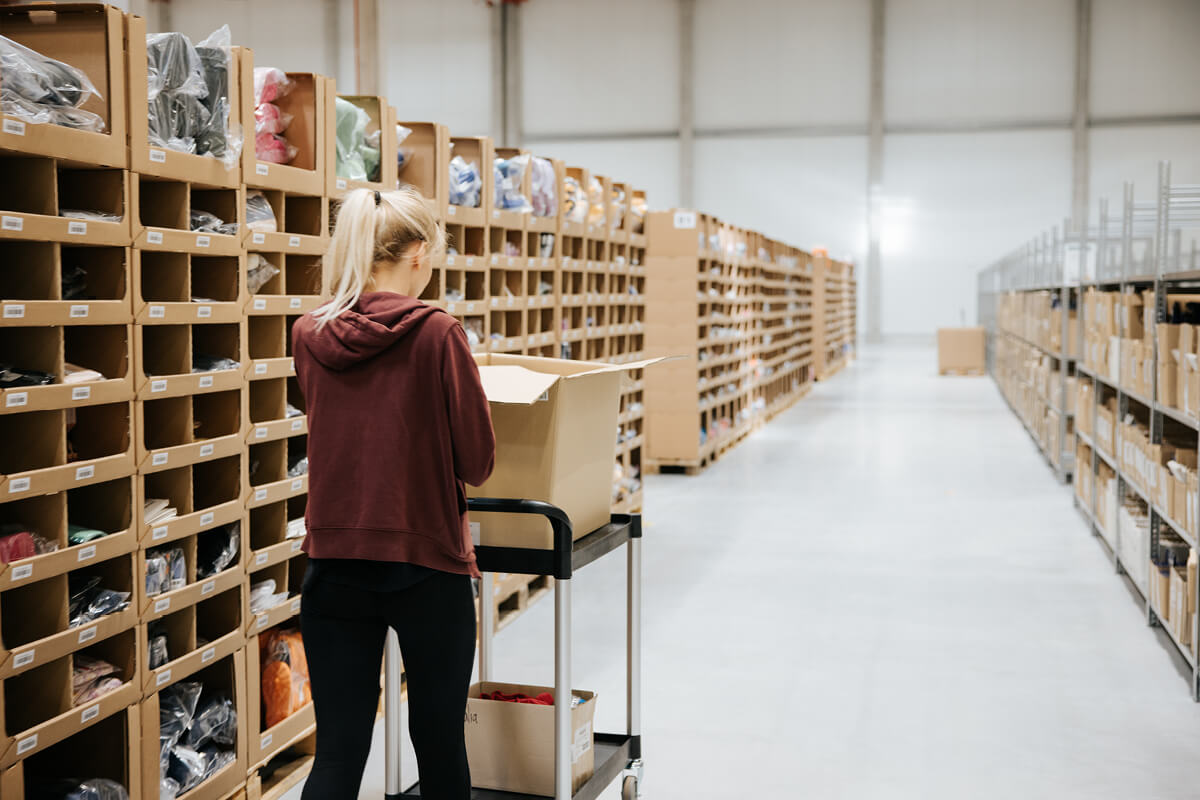
WMS introduction in record time: PSIwms shows comprehensive customer support from the very beginning
The introduction of the new WMS went extremely quickly. Within only ten days the system was put into operation under the guidance of the PSI consultants. The entire implementation process, including analysis, configuration, testing and final rollout, took only four months. Even the integration with the host systems went smoothly.
The implementation was completed in two weeks. In the first week, the system was running at 10% of the order volume, before going fully live in the second week to cover all product movements and warehouse processes.
According to the expert, the decision in favor of PSIwms shows that the customer is comprehensively supported from the very beginning. Before implementation, employees receive a complete training package, the infrastructure is set up and the ready-to-use functions are tested. This ensures a smooth transition, boosts employee confidence in the new system and ensures optimal functionality from the start.
Maximum efficiency with minimum effort
The Hisert warehouse operates in a single-shift system from Monday to Friday. However, the workload increases rapidly towards the weekend, as thousands of orders received between Friday and Sunday have to be processed. More than 70 percent of these orders are line items. Previously, the picking and shipping process took eight hours on Monday. With the introduction of the new WMS, this period was reduced to just four hours in the first week after implementation.
The implementation of the WMS system has made our warehouse processes more efficient and given us more control over goods movements and stock levels. The user-friendly interface of the mobile scanners allowed us to learn the system quickly. Given my previous experience with WMS implementations, I was surprised at how smoothly we were able to master PSIwms.
Hisert emphasizes the smooth transition from analog to digital processes, which can be a real challenge in such comprehensive conversion projects. Immediately after the January implementation, the company's productivity almost reached the level of the busy pre-Christmas period. Two weeks after the launch, inventory of nearly one million items was taken in the distribution center. The process took 48 hours and was carried out using the new system. The inventory involved many employees who had no previous experience in warehousing or using MDT scanners, but who performed their tasks with flying colors.
Challenges and proven solutions
Michal Tokarczyk highlights Hisert's openness and willingness to draw on the expertise and experience of PSI's experienced Polish project team as key factors:
"The solutions implemented in the Szczecin warehouse are based on our previous experience and deployments in other warehouses with complex operations. Thanks to the preconfigured version, system implementation can be significantly faster and more cost-efficient for companies that sell or want to sell products in the omnichannel model.
Contrary to expectations, IT solutions do not necessarily have to be heavily customized to offer non-standard features to customers. Sometimes a standard system with basic, proven solutions is the best choice. This is especially true for SMEs, which have access to unique expertise - essentially the result of numerous previous IT projects," the expert concludes his remarks.
Successful transition thanks to proven partnership
Hisert's openness and willingness to cooperate, combined with the expertise and experience of the PSI team, played a crucial role in the success of this project. This smooth transition from manual to digital processes is not always a given in large-scale conversion projects. The implementation of PSIwms led to an increased efficiency of the warehouse processes at Hisert and enabled a better control of goods movements and stock levels.