Steel plant’s operations are complex because all production steps are interdependent. A successful transformation to net-zero will require simultenously digital optimization production of processes. The result is savings in energy consumption, which in turn reduces emissions and complies with CO2 regulations while staying competitive with changing market demands.
Steel is vivid and a core pillar of today’s society. It is also one of the most important engineering material to build the infrastructure for sustainable energy, the future mobility as well as climate neutral buildings. However, today steel is one of the heaviest industrial CO2 emitter, accounting for about 8 percent of the global carbon emissions.
Steelmakers now face several challenges like,
- government regulations,
- increased cost of CO2 certifications,
- changing customer demands for more environmentally friendly products and
- increasing investors’ interest to decarbonize steel production.
The current energy crisis further intensifies the need for more optimized production management solutions for metals producers.
In response, PSI Metals offers software that metals producers can use to efficiently optimize their processes and energy consumption and in turn reduce carbon emissions. Many global producers use this solution as part of their digitalization and decarbonization journey.
Online heat scheduler generates optimized heat schedule
Heats and casting sequences form the basis for online and reactive scheduling of heats and production equipment allocation in the melt shop. These casting sequences are received from the planning systems and managed in the Schedule Execution Management on the shop floor.
Based on this input, Online Heat Scheduler (OHS) creates a detailed work schedule for all planned heats, which consists of all required treatment and transport steps, their durations, and the assignment of required production facilities and operating equipment where these treatments can be performed. Based on these schedules, energy as well as raw material demand forecasts are calculated and considered. OHS automatically reacts to all changes and delays during production to ensure the delivery of the heats of a sequence to the caster at the required time.
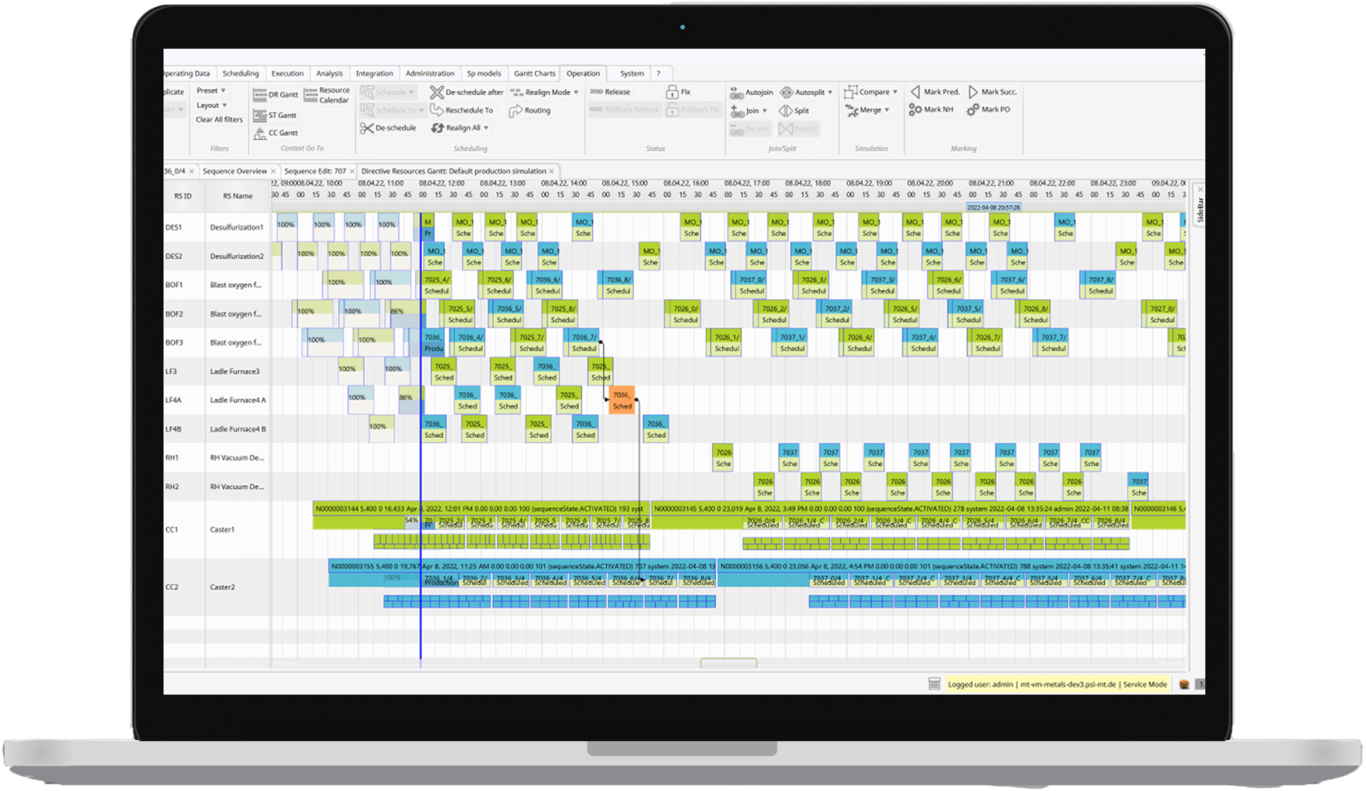
The KPI-based heat schedule optimization enables early prediction of bottlenecks and the impact of production delays. It further supports in decision-making by finding the right balance between economic and ecological melt shop planning. This is an important feature for metals producers on their transformation path to decarbonize steel production.
Melt shop optimization offers cost savings potential for steel producers
During production, unpredicted breakdown can result in sequence interruption and more energy consumption thereby increasing CO2 emissions. OHS is designed to enhance the continuous supply of the caster lines and prevents casting discontinuity. A mathematical model optimizes the navigation of all heats through the facilities of the melt shop. It then displays the respective restrictions with regard to throughput optimization and coordination of bottleneck. The plant manager can see the availability of ladles and lines/facilities. In addition,
- planned maintenance work and plant problems,
- Hot Metal, DRI or oxygen availability,
- energy demand forecast
- including the current energy situation
can be displayed and taken into account.
Processes in future hybrid steel plant will become more complex in forecasting Hot Metal, Scrap, Direct Reduced Iron (DRI) and Energy. The results of this steel plant optimization are savings in production and material costs plus increased decarbonization goals of steelmakers. Some global steelmakers have successfully integrated OHS in their steel plants.
Towards green KPI-driven steel plant optimization
Besides the pressure to decarbonize steel production, recent studies reveal that 14 percent of steel companies’ potential values are at risk if no active measures are taken to decarbonize the industry. Hence, the need for green melt shop optimization that is driven by targeted KPI (Key Performance Indicator).
For this, PSImetals OHS, which is available on the Service Platform (SP) offers features that support steelmakers to achieve green KPI-driven melt shop.
In this way, the hot connect rate can be increased, media consumption can be forecasted, and these forecasts can be made available to energy management systems and utilities. To provide the best possible support to customers, PSImetals OHS SP has a stand-alone service architecture via PSIbus standard interfaces, allowing for a simplified integration into existing IT landscapes.
AI-based decision support in the steel plant
Companies rely on data and KPIs in order to achieve their strategic production and business goals. PSIqualicision was designed to ensure and optimize the process quality by means of intelligent data collection, analysis and balance between goal and criteria conflicts.
The AI-based decision support by OHS/PSIqualicision, involves three simple workflow steps structured to optimize process quality. These include first, automatically analyze inputs/set up constraints and business goals, then run the solver, analyze and balance KPIs with Qualicision AI, and finally iterate, compare and release Qualicision AI-based scenario management.
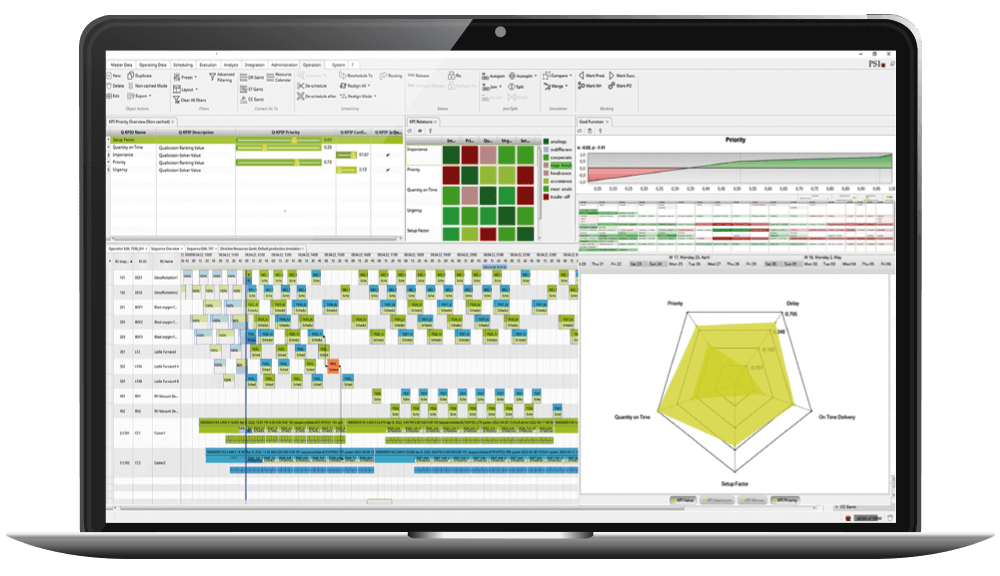
Optimization of times reduces energy consumption and the CO2 footprint
Scenario Management means that the operator can simulate different scenarios to solve a problem. This could be in the forms of adding re-work steps, changing the sequence of heats or shortening treatment, transport or buffer times. Optimization in terms of production time has significant impact in reducing energy consumption, which immediately reduces CO2 emission. Scenarios can be compared to find the right solution.
Balance between economic and ecological steel production benefits
For increased business growth and decarbonization benefits, strategic business and production goals are measured against a specific KPI goal. Automated evaluations of the raw process data are used to create qualitative labels for optimization. A KPI-oriented Qualitative Labeling is generated. It further analyzes business processes according to incompatible KPIs and non-symmetrical goal relations while also improving the learning sensitivity analysis of the adjustable KPI preferences.
The solution offers combinations of benefits that ensure increased efficiency in heat scheduling. For example, the tap-to-cast time can be optimized. Reliable time management ultimately also enables lower tapping temperatures and thus significant energy and CO2 savings.
What do you do in case of production disruptions? For this purpose, the relaxation of “hard” constraints is also taken into account, where the scheduler indicates possible delays in the handover to the caster. This provides the operator with a transparent overview of the current and future planning situation at all times and gives him enough time to compensate for disruptions and time losses.
Steel production at the crossroads of decarbonization and digitalization
Decarbonization and digitalization are keys to some of the industry’s challenges. Although software cannot change the steel making process, digitalization of the process, like the use of the new PSImetals Online Heat Scheduler with integrated PSIqualicision AI Solver, helps in decarbonization while reducing resource and production costs.