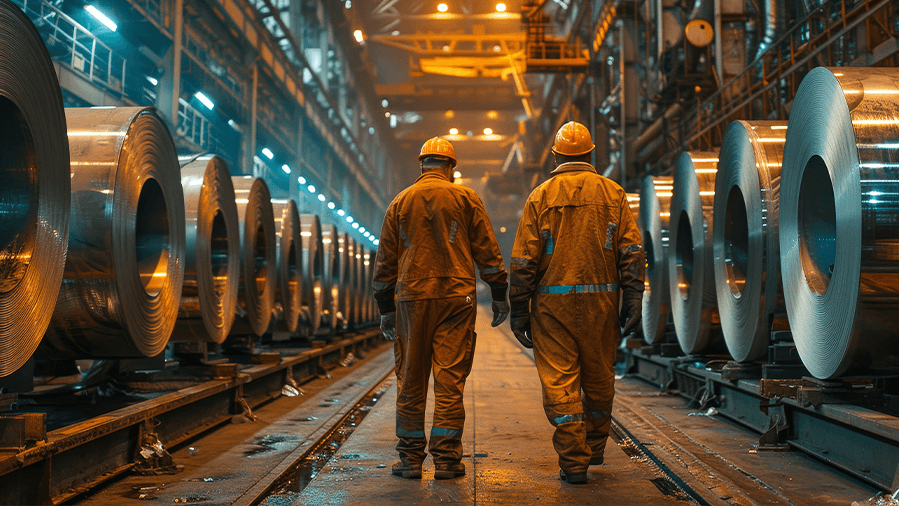
Case Study Preventing nonconformities with PSImetals quality indicators
Quality forged, durability ensured, customer satisfied.
Ensuring steel products meet the highest quality standards is crucial in today’s competitive market. PSImetals Quality Indicators (QI) offer a sophisticated solution for quality control based on comprehensive process data aggregation and evaluation. This case study explores how PSImetals' QIs have improved the quality control process in steel manufacturing.
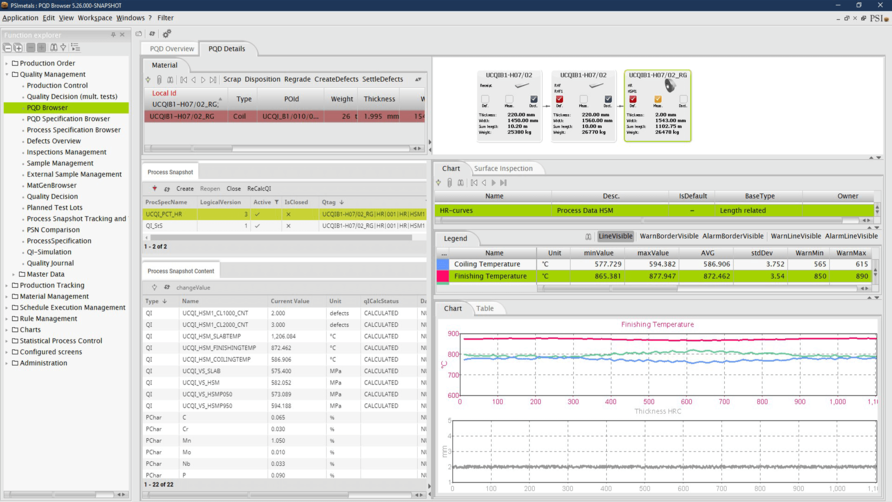
Steelmaking requires rigorous quality control procedures to ensure that products align with customer specifications. Direct and immediate assessment of all process features and their interaction is often impractical. PSImetals Quality Indicators address this challenge by synthesizing numerous parameters into single, actionable values, configured to reflect the manufacturer's knowledge of product and process quality.
Challenges
Final steel product quality is a result of the interaction of various product and process parameters throughout the production route. Controlling each parameter individually within industrial tolerances does not always guarantee high-quality results. Cross-line quality control, however, is a complex task that requires not only comprehensive product knowledge but also the precise collection of process data from multiple sources. Additionally, traditional quality control methods often involve lengthy and labor-intensive testing processes, especially for semi-finished products like continuous cast slabs or blooms. While metallography methods, for example, are precise, they are not feasible for real-time quality assessments, leading to delays that can hinder production efficiency and increase costs.
Objectives
- To leverage existing process data for real-time quality assessments
- To reflect the complexity of the influence of process parameters on final product quality
- To translate metallurgical knowledge into automated, cross-line quality control
- To reduce time and effort involved in quality inspections
- To identify quality issues as soon as possible and minimize downgrades and delivery delays
Solution approach
PSImetals Quality Indicators (QI) utilize material-specific process data from various production steps. QIs convert high-resolution, complex data sets into single values, allowing for immediate quality decisions.
For example, in continuous casting, parameters like casting temperature, temperature distribution, mold level fluctuation, and casting speed are used to determine slab quality without requiring metallographic analysis. This method relies on proven correlations between these process parameters and material quality, calculating the essential quality indicators in real-time.
Process data from several production steps can also be mapped along the production route and combined into QIs. For example, hot rolling, cold rolling, and annealing data can be used to evaluate the homogeneity of the mechanical properties of a steel strip throughout its length.
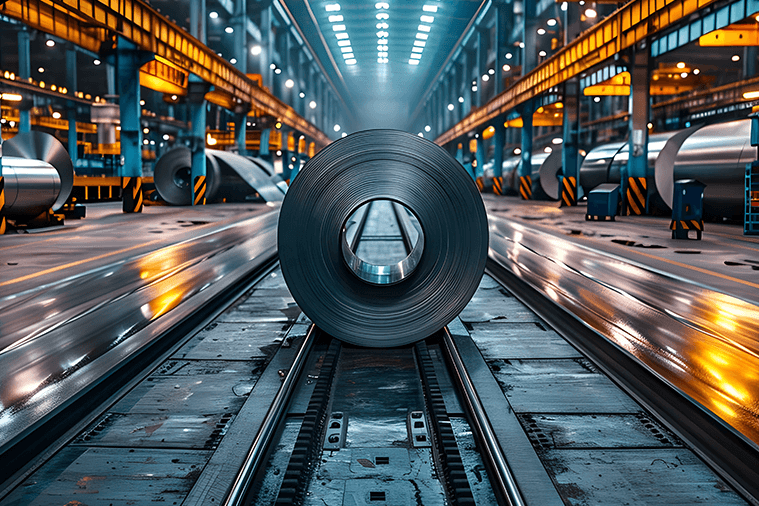
The result
The implementation of PSImetals QI has significantly improved the efficiency and reliability of quality assessments. By using process parameters to derive Quality Indicators, steel producers can now make informed and automated quality decisions immediately after each production step. This advancement leads to:
Conclusion
The introduction of PSImetals Quality Indicators has enhanced the quality control process in metals production, ensuring that products meet stringent standards efficiently. PSI will further extend the use of Quality Indicators to include product-based sustainability monitoring. Additionally, the integration of Machine Learning models for Quality Indicator calculation is also planned.