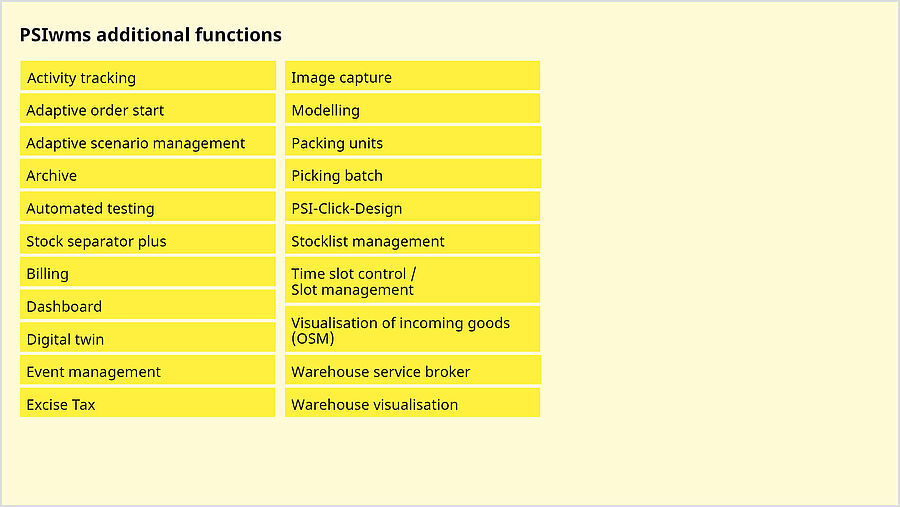
PSIwms - Module PSIwms specific additional functions
Alongside the additional functions provided in accordance with the VDI 3601 guideline, PSIwms also includes other specific additional functions for controlling warehouses.
The PSIwms specific additional functions provide, for example:
- Safe migration of legacy systems
- Simplified handling of recurring situations
- Minimization of misconfigurations
- Sound decision-making basis with regard to whether to open or close an external warehouse or another location
- Use of pre-configured scenarios which have been created by experts
- Ensure performance by shifting the burden away from the production database
- Earlier recognition of critical situations so that the necessary action can be taken in good time
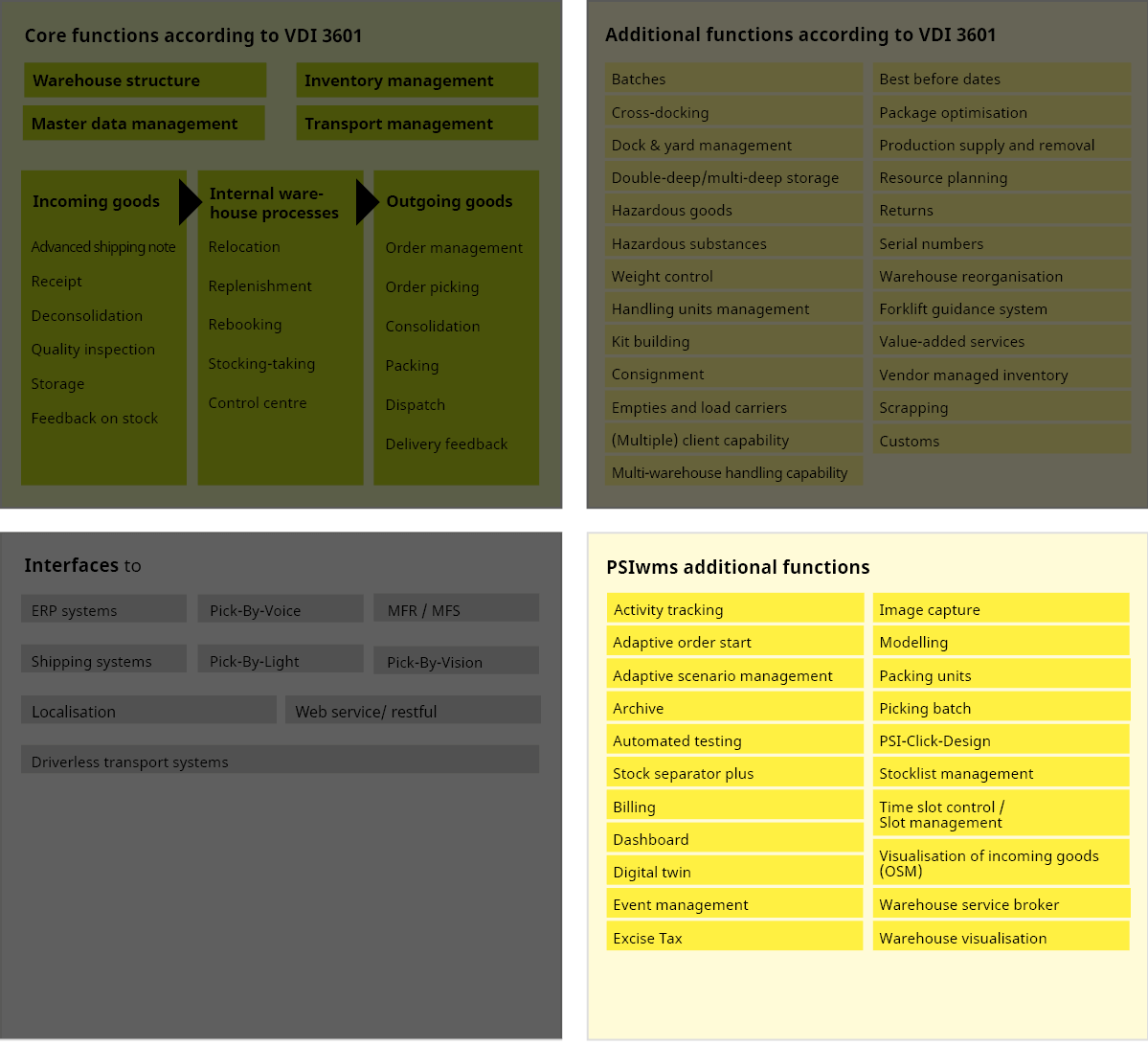
Features
-
Activity tracking Configurable logging of activities in the warehouse to record process times as a basis for dashboards, key performance indicators and BI tools.
-
Adaptive order start PSIwms adaptive order start enables a KPI-oriented dispatching of orders, taking into consideration current capacities. This means that PSIwms automatically starts orders or intentionally holds back orders with the aim of achieving a uniform utilization of all warehouse areas and possibly other resources, such as packing stations.
-
Adaptive scenario management Various scenarios can be defined in PSIwms. These determine how PSIwms behaves in a certain situation. For example, the two scenarios “early shift” and “late shift” can be defined, which may differ due to difference in storage and/or picking management. Essentially, almost all configurations in PSIwms.
-
Archive In order to access operating data as efficiently as possible, PSIwms makes a distinction between data for operational use in the production database, and data for archiving and long-term analysis in the archive database. The archive function automatically moves the configured data for archiving at regular intervals from the production to the archive database. A convenient button allows you to switch between archive and production mode in the PSIwms.
-
Automatic testing In order to prevent errors when launching software or during a later modification, an automated test process (SPU test) has been integrated in PSIwms, with the result that your system automatically undergoes concurrent testing. These rely on a pre-defined test database, as well as defined, reproducible conditions. Changes can therefore also be tested while the system is in operation. 100% tested software is especially important here.
-
Stock separator plus Stock (also “bin quantity”) describes the quantity of an item with identical attributes which are found together on the same transport unit. Essentially, all possible combinations of stock attributes and stock separators can be configured in PSIwms. The stock separators are duly considered when stock is moved.
-
Billing The billing module is used to create invoices for the services provided by a warehouse operator. This is based on the statistics recorded in PSIwms. Value added services such as, for example, repacking/labelling of goods, cleaning/repair of carriers etc. can be recorded by the service codes in PSIwms and charged to the customer via the billing function.
-
Dashboard Alongside the configuration of several large cockpit screens in Ultra-HD-4K resolution, the new PSIwms myCockpit enables individual cockpit elements to be displayed on any screens. This helps to visualise e.g. spreadsheet data with diagrams. Further benefits of PSIwms myCockpit include the option of transferring parameters to cockpit elements, as well as direct input of a database request in the cockpit element wizard.
-
Digital twin Configurable data transfer from a production system to a test system to test real data with optimized process configuration or new software versions by means of automated tests.
-
Event management If there are a number of processes running in parallel, PSIwms supports the user in tracking the process through event management. Any occurring events can be configured, recorded and classified. This expansion module can be used, for example, to monitor the processing of shipping notifications within a certain period, to check that transport units are warehoused within a certain period or that orders are completed within a certain period. If required, emails can be sent to defined consignee groups if events occur, reports can be sent to a host system, or alarms displayed in the cockpit.
-
Image capture The Image Capture expansion module allows photos to be captured via a camera with items, shipping notification, orders or invoices. Therefore, defective goods for example can be documented in PSIwms on delivery. This documentation can then be produced as evidence if there are any claims at a later date.
-
Picking batch Picking orders can be divided into separate order picking orders between areas, as well as grouped into areas for commissioner batches. This is an optimisation of the picking itself (by reduction of paths or single picks) or downstream processes such as consolidation or packing. A picking batch is carried out with multi-stage picking (e.g. in combination with sorter) or multi-order picks (e.g. in combination with the target pick-and-pack container).
-
Warehouse visualisation PSIwms has a process-based warehouse visualization feature which provides you with concise information at a glance on the status of the entire warehouse. Fill levels of warehouse sections, allocation of items to storage areas, allocation of removal orders across all warehouse sections, and much more, are highlighted in the visualization, therefore providing cockpit with optimization potential. A design mode allows detailed modelling of your own warehouse, and a link to PSI Click Design allows you to design the visualization dialogue according to the specific user (e.g. with regard to input fields and function buttons).
-
Modelling PSIwms allows the user to model all processes, goods flows, topologies, parameters in a separate configuration tool or via the dialogue in the PSIwms client. A variety of solutions can therefore be created through simple or complex rule bases, without having to make a change through programming. Even when live, it is easy to reconfigure or extend the warehouse flexibly through the PSIwms modelling.
-
PSI click-design PSI-Click-Design enables you to create your own screens and overviews using an intuitive visual editor. You can create your own dialogue combinations, your own detailed screens and your own filter definitions to suit the specific user and save them in profiles. It includes new grouping and aggregating functions, docking and release of dialogues, and improvements for use of Ultra HD 4K resolution.
-
Stocklist management Hierarchical structures between items and/or other bills of material can be created by an item-item allocation. Therefore, substitutions or sub-items can be defined along with bills of material (e.g. several items for one kit).
-
Excise tax Selective storage of untaxed goods - Warehouse for taxed or non-taxable goods - Maintenance of a tax book - Recording of all tax-relevant movements in the warehouse - Mapping of tax-relevant attributes in the article - Customs tariff number - New tables of rule for determining tax rates - Tracking of tax documents
-
Packing units A packing unit is a unit in which the items are packed, e.g. a bag, container or box. PSIwms can manage various packing units for items and transport units. Up to three of these units can be nested. The packing units are taken into account in all warehouse processes, therefore a distinction can be made in picking, for example, between full packing units and partial quantities.
-
Visualisation of incoming goods (OSM) The PSIgis component of PSI Java Framework allows you to visualise any number of locations and routes using OpenStreetMap. In PSIwms, this is used mainly to display consignees of active orders, or to display IOT chips which enable tracking and tracing of valuable transport units or empties.
-
Warehouse service broker The warehouse service broker additional module serves as an intermediate level below the ERP systems to coordinate the WMS systems of several locations – regardless of the manufacturer of the WMS software solution – and combines the WMS systems into one large virtual warehouse. In doing so, warehouse service broker draws its data from the relevant host system via the interface, and also enables processing along with simple information retrieval. Stock transfers can thus be notified in the sub-systems, inventory changes reported to the relevant host and orders forwarded. The sub-systems are synchronized via a central point. You can continue to operate them via the existing WMS.
-
Time slot control / Slot management Slot management is used for planning and control of the warehouses' loading and unloading transport.