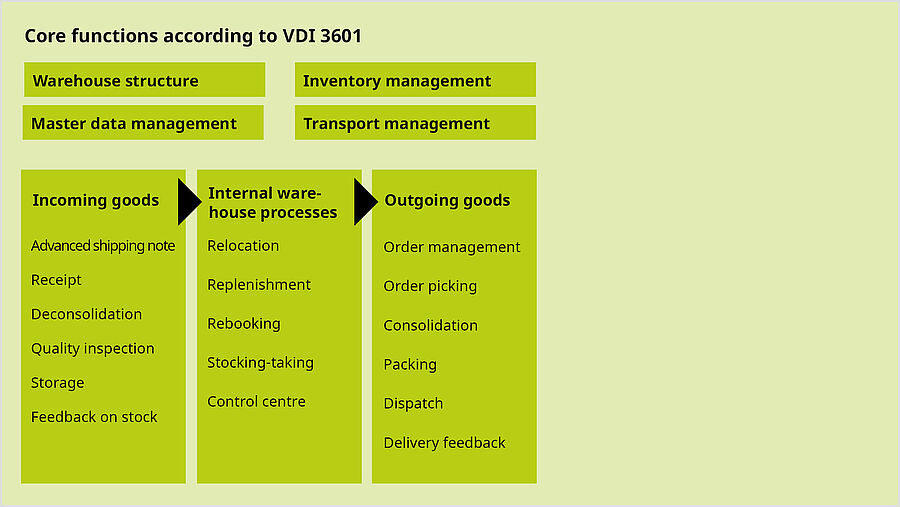
PSIwms - Module PSIwms core functions
PSIwms basic module includes the essential core functions of warehouse management and management processes which relate to the warehouse.
The PSIwms core functions provide, for example:
- Error-proof and reliable process handling
- Increased transparency in the warehouse
- Targeted resource scheduling
- Reduction of turnaround times
- Increased delivery reliability
- Faster modification of processes
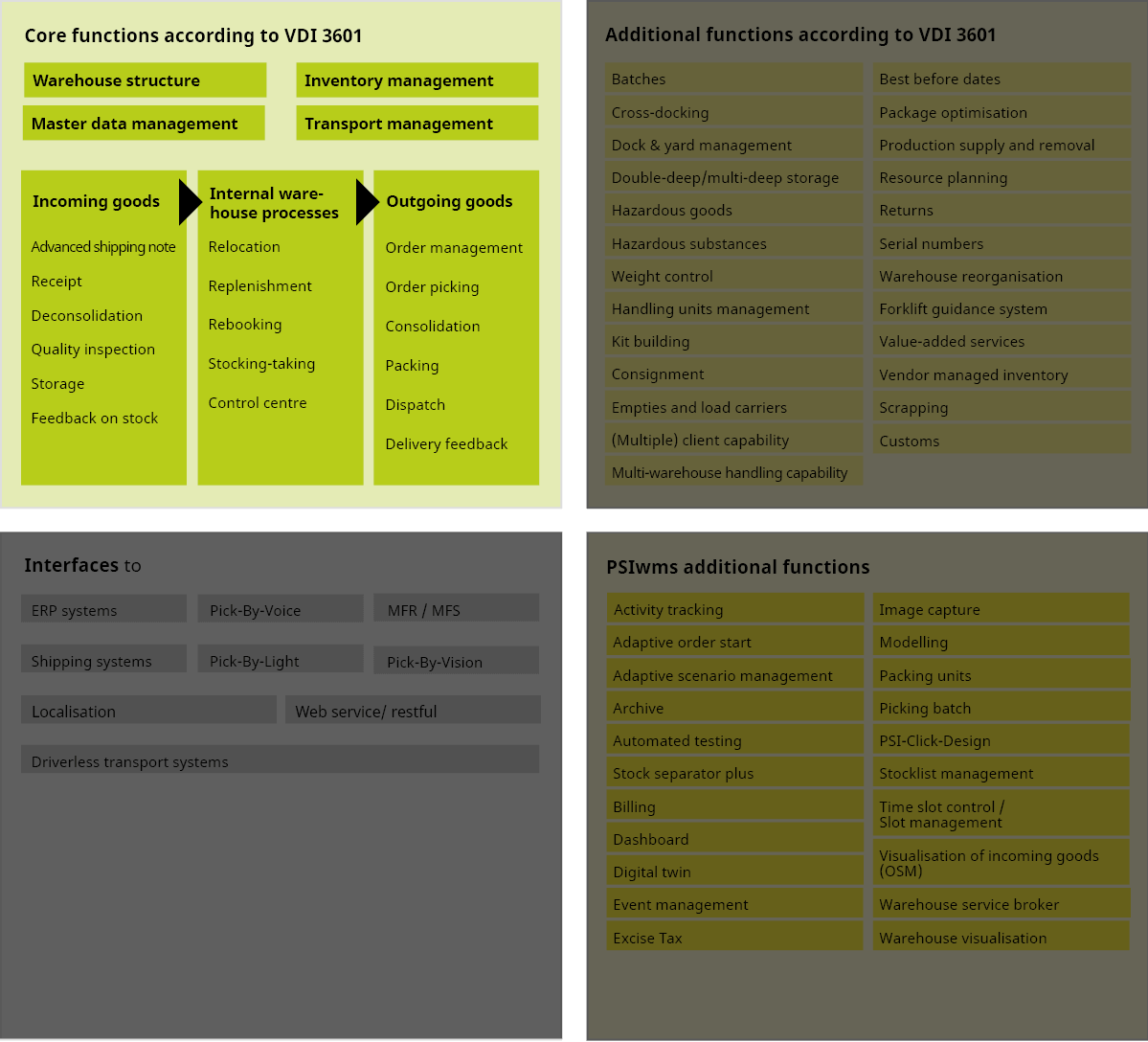
Features
-
Warehouse structure PSIwms can show any number of warehouses of a company, which consist of various linked logical or physical organizational units, such as locations, warehouse types, warehouse sections, warehouse subsections, warehouse areas, bays, movement areas, picking areas, activity areas, work stations etc. The configuration of the warehouse structure is abstract and kept simple to provide flexibility when making changes, even when in live operation.
-
Inventory management Stock management is responsible for managing the item master and warehouse stocks, for searching for stock which matches specific search requests, as well as for sending posting functions/reports to the ERP system via the interface. A variety of stock separation attributes enable you to differentiate stocks or to merge identical goods into one stock.
-
Master data management Business partners, plant calendar, quantity units, clients, plants, locations, countries, on-hold reasons and reservation reports mostly form part of the basic data. Basic data can apply to one or to all locations. The data can either be exchanged via ERP system interfaces or entered in the PSIwms modelling or the PSIwms client basic data dialogues.
-
Transport management PSIwms enables management of transport orders which carry transport units in the warehouse from a source to a destination. Various transport systems (forklift, conveying equipment etc.), route parametrisation (allocation of transport system /transport equipment to route sections), and space capacities are taken into account.
-
Advanced shipping note Notification of incoming goods is normally provided in the form of shipping notifications and includes information on the goods such as supplier, consignee, order items with article number and quantity etc. Shipping notification can include raw quantity figures, complete transport units with NVE and stock information, as well as units without stock information. Unscheduled incoming goods without shipping notification can also be accepted by entering the delivery note information into PSIwms dialogues.
-
Receipt During receipt, goods in the incoming area are transferred to the system as stock and are then available for further processes. On receipt, the received goods are also checked against the shipping notification, for example by scanning barcodes, reading RFID tags or manual entry.
-
Deconsolidation Deconsolidation is the process of splitting or breaking down delivered goods into transport units which can be stored in the warehouse sections, or which are needed for special processes such as quality inspection or cross docking.
-
Quality inspection The quality inspection may take place in the incoming goods area as required or in separate warehouse sections, and cover either the total quantity or a random sample. Depending on the shipment, various quality inspection requirements can be sent to PSIwms via the ERP system interface.
-
Storage Warehousing from incoming goods into the warehouse section includes searching for storage space whilst following the specific warehousing strategies (for example, addition of stock, fixed area, empty space search etc.) and other criteria such as physical dimensions, item classification, transport unit types, ABC classification, current stock situation in the warehouse etc.
-
Feedback on stock The shipping notification can be closed or the stock feedback sent to an ERP system at various points in the incoming goods process. For example, feedback can be sent with a record of each shipping notification item, the complete shipping notification or of the warehousing in the storage area.
-
Relocation Stock transfers are transportation of stocks which are triggered manually or automatically, and have either specified a fixed destination or perform a destination are search similar to that of the storage process. For example, stock transfers of goods to be delivered to dynamic picking areas can be requested by the system, or triggered by additional functions, like the many stock transfers in warehouse re-organisation.
-
Replenishment Replenishments are special stock transfers which are triggered by various criteria such as minimum and maximum stock quantities or order quantities and are then performed dynamically in the destination area (e.g. picking areas) or in fixed destinations (fixed-item areas).
-
Rebooking Allocations are changes to the stock attributes, e.g. quantity, stock qualification (e.g. blocked, released, QA on-hold etc.), special stock type (e.g. consignment stock, customer allocation, etc.) and much more. Allocations can be initiated by users and performed in PSIwms or via the ERP system. Allocations can follow physical stock transfers or may arise as a result of these, for example if stock is changed to consignment stock and this may only be managed in a separate warehouse section.
-
Stock-taking Inventory management in PSIwms is responsible for taking the permanent inventory, annual inventory or random inventory according to the requirements of the ERP system. The inventory strategy can be defined for different areas or warehouse sections. This determines for example whether a paper list, a PSIwmsclient dialogue or a mobile data terminal should be used for the inventory taking by the warehouse operator.
-
Control centre All processes or system statuses can be monitored in the cockpit via the PSIwms PC client, and actions can be taken to control the operating processes. For example, stock transfers can be triggered, orders started or cancelled, material flows or picking tracked, interfaces monitored etc.
-
Order management The removal of the stock located in the warehouse is controlled by delivery orders (with order items), which can be sent via the ERP system or entered directly into the PSIwms client. The order data is checked according to the configured criteria in the system and is a requirement for approving the subsequent order processing steps. As an option, several delivery orders can be automatically merged to form bulk orders according to the defined criteria. The correct stock in the warehouse is reserved according to the order items, and packages are created in the rest of the process. These are in turn allocated to cargo or dispatch routes.
-
Order picking Picking is the process step during which the reserved stock from the warehouse stock is compiled and supplied to the subsequent process steps – consolidation, packing and shipping. Various picking processes (person to goods, goods to person, single order, multi order etc.), communication with the resources involved (conveying equipment, forklifts, warehouse staff etc.), and route-optimised picking are also supported. Case calculation in PSIwms is used for further optimisation of the picking lists. Case calculation is a multi-critical tool for fill-level optimisation of picking bins and trolleys.
-
Consolidation Consolidation is the physical assembly of the picked stock and can be performed during picking (pick & pack process), or in a separate process step in a specially provided physical warehouse section.
-
Packaging The packing process normally follows consolidation and is supported in PSIwms by many functions, e.g. packing selection, repacking functions, weight check, counting or serial number capturing and printing of labels/documents. Case calculation also automatically optimizes the package size during the pick & pack process.
-
Dispatch Packages ready for shipping are prepared in dispatch areas during the shipping process, loaded onto the allocated routes, and the necessary shipping documents are printed. When allocating the route, the case calculation provides the option of optimising the utilisation of the transport vehicles. An interface to an external shipping system with an online link to the CEP service provider can also enhance the shipping process through a number of functions.
-
Delivery feedback Feedback on the delivery orders and the change in the stock situation can be sent at configurable times. There is also an option to send this multiple times to the ERP system with different statuses. The subsequent processes can be triggered depending on the feedback, e.g. replenishment, invoice printing etc.