Stahlhersteller sind bestrebt, ein ausgewogenes Verhältnis zwischen Produktqualität und Herstellbarkeit zu erreichen. Dies führt zu einem Dilemma, mit dem viele Qualitätsingenieure seit langem konfrontiert sind. Der Einsatz von industrieller Künstlicher Intelligenz bietet jedoch eine elegante Lösung, die als "Forward Dressing" bekannt ist.
Die Produktion in der Stahlindustrie ist ein komplexer Prozess. Dabei werden nicht nur viele verschiedene Stahlsorten, Abmessungen und Oberflächenbehandlungen in Tausenden von Varianten kombiniert, sondern auch die Produktionswege bestehen in der Regel aus mehreren aufeinanderfolgenden Schritten mit sehr spezifischen Prozess- und Qualitätsanforderungen.
Die inhärente Komplexität einer solchen Planungs- und Prozessdynamik trifft auf einen stetig wachsenden Marktdruck (Kunden, Wettbewerber und Rohstofflieferanten). Dabei entstehen sehr unterschiedliche Anforderungen wie
- Kostensenkung
- Qualitätsverbesserung
- Minimierung der Lagerbestände
- Einhaltung von Lieferterminen
Es liegt auf der Hand, dass es in einem solchen Umfeld keine Einheitsgröße für alle gibt. Die Spezialisierung der Produktion ist nicht nur eine Herausforderung für die Planung, sondern auch für die Qualitätskontrolle.
Dazu werden Qualitätsüberwachungsmethoden wie die Statistische Prozessregelung (Statistical Process Control, SPC) eingesetzt, um zunächst Prozessschritte zu identifizieren, die nicht den zentral durch das Fertigungsleitsystem (Manufacturing Execution System, MES) vorgegebenen Anforderungen entsprechen, und danach, falls notwendig, die entsprechende halbfertige Materialeinheit vom Fertigungsauftrag abzubinden.
Die Qualitätskontrolle in einzelner Prozessschritten ist begrenzt
Methoden wie die statistische Prozesskontrolle, die auf einzelne Prozessschritte und Anlagen angewendet werden, können sehr effektiv sein. Sie beruhen jedoch auf den Annahmen, dass:
- das Eingangsmaterial Standardeigenschaften aufweist. Das bedeutet, dass es unter nahezu idealen Bedingungen hergestellt wurde und daher nur geringfügig vom erwarteten Idealzustand abweicht.
- die vordefinierten Toleranzen der Fertigungsparameter, sofern sie nicht überschritten werden, das gewünschte Ergebnis gewährleisten
Bei näherer Betrachtung dieser Annahmen ergibt sich ein Widerspruch:
- Einerseits fordert eine Fertigungsanlage, die Halbzeuge verarbeitet, dass diese in den vorangegange-nen Produktionsschritten engste Toleranzgrenzen eingehalten haben, um ein nahezu idealer Ein-gangsmaterial darzustellen.
- Auf der anderen Seite wünscht die Fertigungsanlage, die Halbzeuge liefert, möglichst breite Toleranzgrenzen, um die Produktion zu erleichtern und damit sowohl Ausreißer als auch Abwertungen zu minimieren.
Allerdings ist das gleiche halbfertige Materialstuck, das einer Analge zugeführt wird, natürlich auch der Output der vorhergehenden Analge, so dass ein "vernünftiger" Kompromiss zwischen Qualität und Herstellbarkeit die typische Wahl für die Festlegung der Toleranzgrenzen ist. Das funktioniert fast immer, aber leider nur fast.
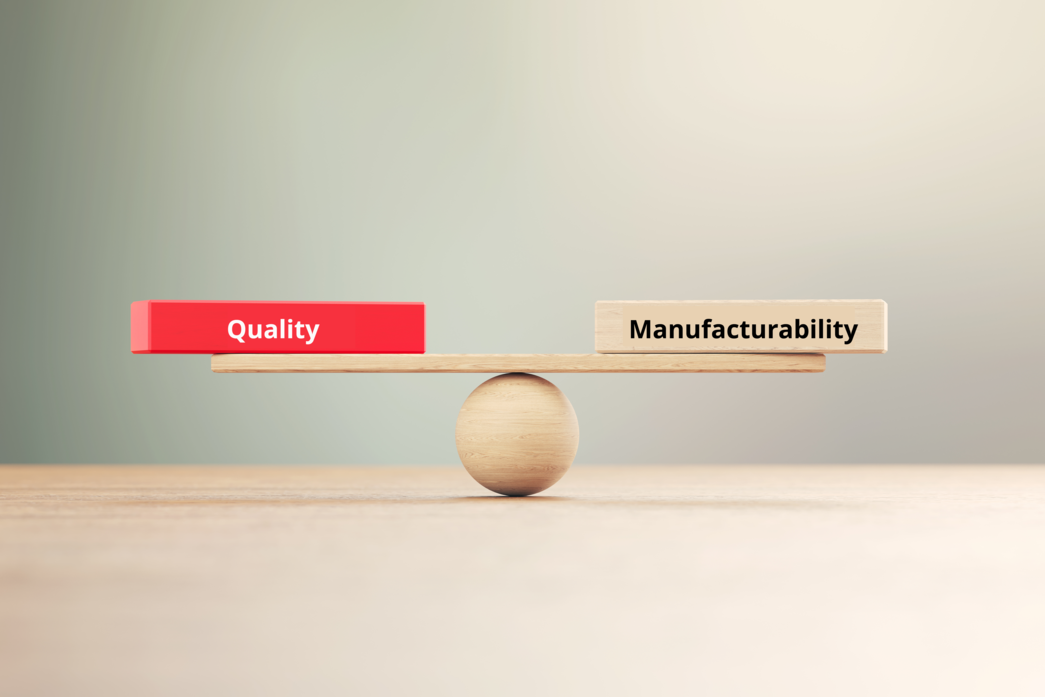
Wie die Stahlproduktion mit vordefinierten MES-Qualitätszielen scheitern kann
Dieser Balanceakt soll an einem vereinfachten Beispiel verdeutlicht werden, bei dem die Streckgrenze eines Endproduktes nur durch die chemische Zusammensetzung der Schmelze und die Temperaturführung in den nachgeschalteten Fertigungsschritte beeinflusst wird.
Für eine bestimmte Stahlsorte wird dem Schmelzbetrieb eine definierte chemische Zusammensetzung vorgeschrieben, indem Zielbereiche für den Gehalt an Legierungselementen und Höchstgrenzen für den Gehalt an Spuren und Begleitelemente festgelegt werden. Je größer die Intervalle sind, desto einfacher ist die Produktion für das Stahlwerk: getroster Einsatz von Standardverfahren, weniger Korrekturbedarf, weniger Beschränkungen in der Schrottzugabe - letztlich höhere Produktivität bei geringeren Kosten. Unter diesen Bedingungen ist jedoch zu erwarten, dass die Streuung der chemischen Zusammensetzung der Schmelzen groß ist, obwohl alle Schmelzen mit der gleichen Qualität gekennzeichnet sind.
In den nachgeschalteten Anlagen ist die automatische Kontrolle der Temperaturen nicht immer einfach. Auch hier gilt: Je breiter die Zielbereiche für die Temperaturen sind, desto weniger Ausreißer gibt es auf der Ausgabeseite und desto größer dürfte die Streuung der Ist-Temperaturen sein.
In den meisten Fällen ist der Gesamteinfluss der Streuung der chemischen Elemente und der Temperatur auf die mechanischen Eigenschaften mäßig, da die tatsächlichen Werte eher normal verteilt sind. Dies ist jedoch nicht immer der Fall. Eine relativ harte Schmelze, die alle Spezifikationen für die chemische Zusammensetzung erfüllt, kann am Ende bei relativ niedrigen Temperaturen (noch innerhalb der jeweiligen Temperaturzielbereichen) verarbeitet werden, sodass sich diese „härtenden“ Effekte zu einer unerwartet hohen Festigkeit addieren, die möglicherweise außerhalb des Zielbereichs liegt (Abbildung 1).
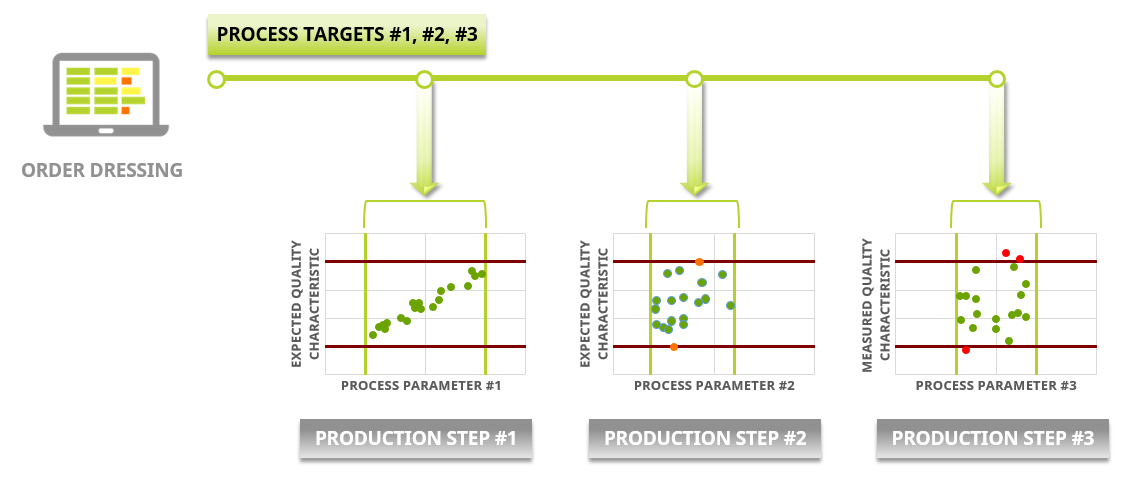
Andererseits können sehr enge Grenzwerte für die chemische Zusammensetzung und die Verarbeitungstemperaturen hervorragende Ergebnisse in Bezug auf die Streckgrenze garantieren. Gleichzeitig würde eine unnötig hohe Anzahl von Prozessausreißern auftreten, die ein Abweichungsmanagement für die angearbeiteten Produkte erfordern.
Solange alle Parameterziele für jede Fertigungsanlage vor der Produktion festgelegt werden (in der Sprache des MES: technische Ausarbeitung des Kundenauftrags durch konventionelle Auftragsklärung), ohne die realen Bedingungen des spezifischen Eingangsmaterials vor jeder Anlage zu berücksichtigen, wird das oben beschriebene Dilemma des Qualitätsingenieurs bestehen bleiben: Es wird immer ein Balanceakt zwischen Qualität und Herstellbarkeit sein.
Forward Dressing: Schnelles Reagieren auf der Grundlage von Wissen
Aber was wäre, wenn die Prozessparameter des nächsten Prozessschrittes für jedes Materialstück auf der Grundlage seiner eigenen „historischen“ Eigenschaften optimiert werden könnten? Könnten wir dann die Prozesse in die "richtige" Richtung lenken, um einen "unausgewogenen" Input zu kompensieren und so die Eigenschaften des Endprodukts in Richtung idealer Werte zu lenken?
Damit ein solch reaktives System richtig funktioniert, muss es auf Wissen und Schnelligkeit basieren:
- Wissen, in Form eines prädiktiven Modells, wertet die vorgelagerte Datenhistorie des einzelnen Inputmaterials aus und liefert maßgeschneiderte Anpassungen der nachgelagerten Prozessparameter
- Schnelligkeit ermöglicht es, alle relevanten Daten für die notwendige Auswertung zu erfassen und ihre korrigierenden Ergebnisse noch termin- und bearbeitungsgerecht einzusetzen
Um auf das obige Beispiel zurückzukommen: Die chemische Zusammensetzung jeder Schmelze, die den Schmelzbetrieb verlässt, würde im Hinblick auf die nach der Standardverarbeitung zu erwartenden Festigkeit des Endprodukts bewertet; falls erforderlich, würden die Sollwerte der Temperaturführung für jede Materialeinheit individuell gemäß dem werksübergreifenden prädiktiven Modell geändert, um ausgleichende Effekte auf die Festigkeit in den nachgeschalteten Fertigungsanlagen (z.B. Warmwalzstraße, Durchlaufglühe, Nachwalzgerüst) zu erzielen. Auf diese Weise sollte nicht nur das Risiko von Ausreißern minimiert werden, sondern auch die Streuung der angestrebten Eigenschaften verringert werden. Mit anderen Worten: weniger Abwertungen und höhere Qualität.
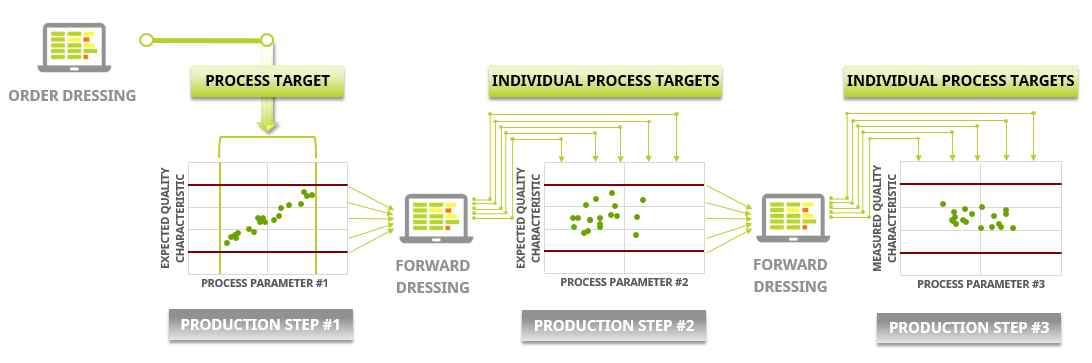
Bei PSI Metals nennen wir dieses selbstregulierende Verhalten vom MES "Forward Dressing".
Laut Wikipedia ist Intelligenz "die Fähigkeit, Informationen wahrzunehmen oder abzuleiten und sie als Wissen zu speichern, um sie für adaptive Verhaltensweisen in einer Umgebung oder einem Kontext zu nutzen".