
Decarbonization & Energy Services
Discover innovative solutions to reduce emissions and drive sustainable metals production.
The complexity of metals production makes it challenging to optimize production, save energy and comply with CO2 regulations. Currently, metals production is undergoing transformation towards green metals production. Hence, transformation to net-zero production needs to go hand-in-hand with process digitalization and innovative software for efficient production management of planning, scheduling and execution of processes. With our production management solutions to support the digital transformation towards green production, we accompany you on the way there. Discover our product portfolio for sustainable production management now!
What you can do with our solutions
- Integrate the management of energy consumption and supply into your existing system
- Support and monitor the decarbonization of metals production processes
- Contribute to the reduction of emissions in transport and logistics within your plant
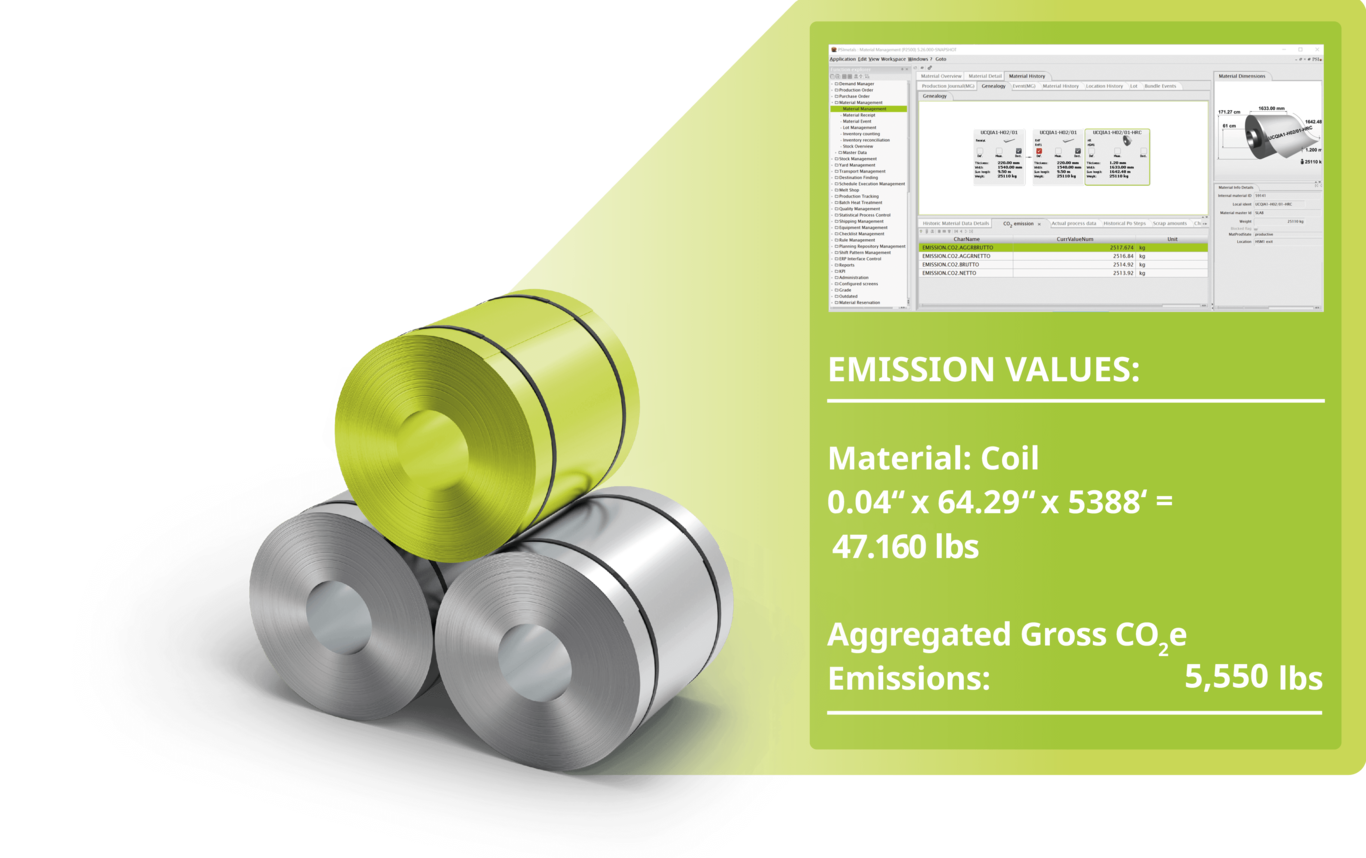
Our goal towards decarbonization – production management solutions today for generations to come
PSImetals Product Carbon Footprint (PCF) Tracking is one of the highlights in our decarbonization product portfolio. The PCF approach provides transparent calculations based on configurable Quality Process Snapshots and tracking of energy consumption and CO₂ emissions at piece and product levels along the entire production chain. It tracks all emission-relevant process data and calculates scope 1, scope 2, and upstream scope 3 CO₂ emissions in real-time!
Benefits at a glance
-
Cost effectiveness
PSImetals enhances cost effectiveness together with sustainability.
-
Efficient KPIs
PSImetals uses economic as well as ecological efficiency KPIs as optimization targets.
-
Flexible infrastructure
PSImetals supports various requirements with a flexible infrastructure that can run services in any environment as needed.
-
Optimization of processes and resources
PSImetals optimizes and balances process flows and resource usage.
Highlights
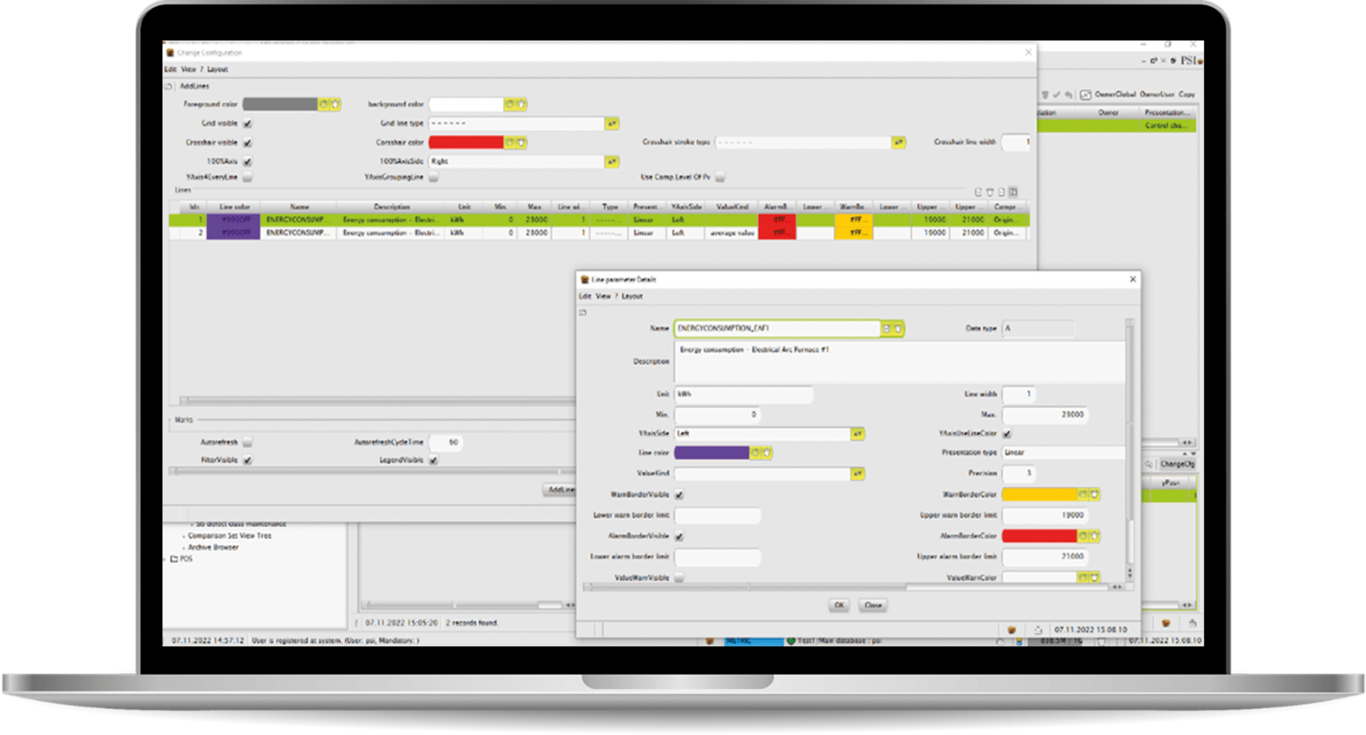
PSImetals Process Value Archiving Management
Process data measured by the automation layer is reported to the Manufacturing Execution System (MES) for real-time monitoring and archiving. This supports detailed tracking of energy and resource consumption, which is crucial for energy management and CO₂ emission calculations. Dashboards and performance reports use historical data for comprehensive evaluations.
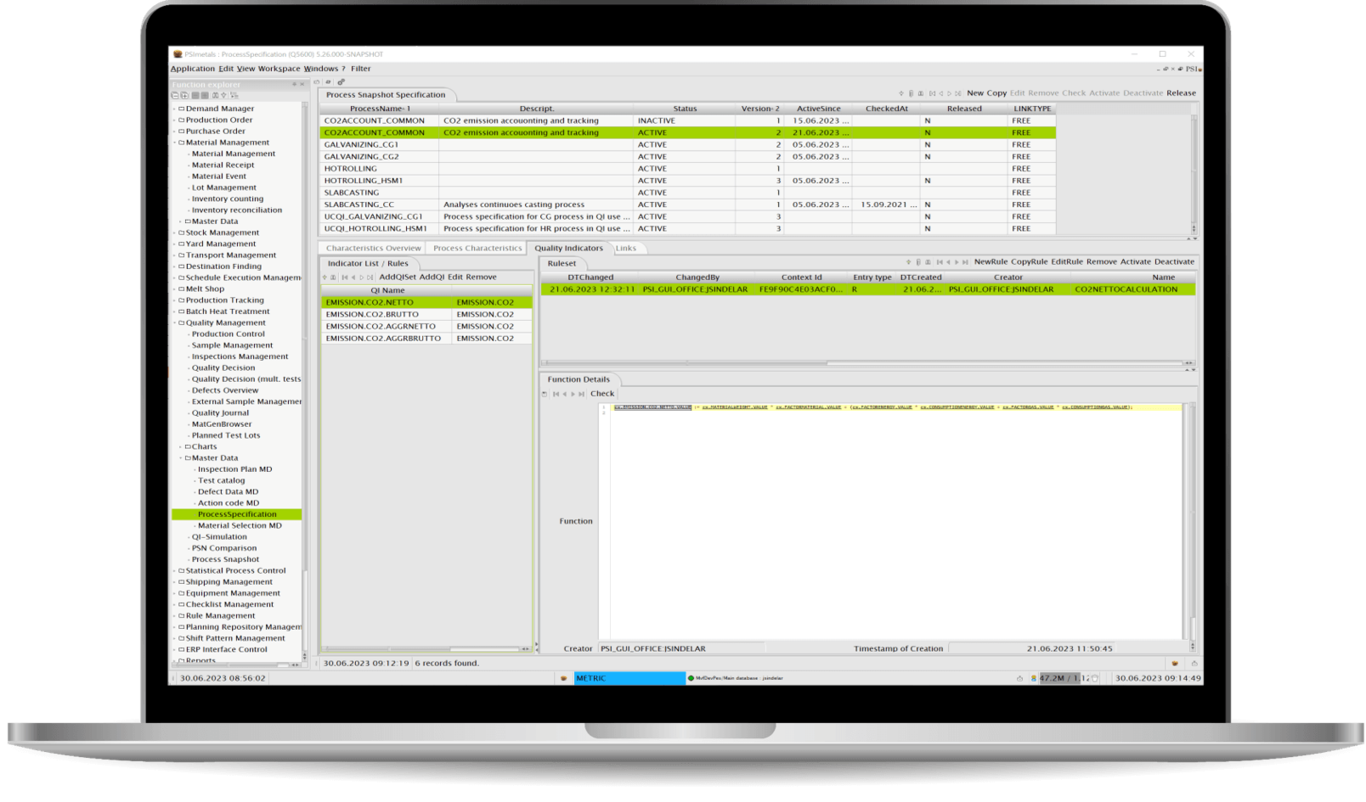
Quality Process with PCF Tracking
PSImetals Quality provides an ideal framework for "cradle to gate" Product Carbon Footprint (PCF) tracking based on process snapshots for calculation of emissions of scopes 1, 2, and 3. It uses hierarchical Green House Gas (GHG) emission factors across production areas, lines, and steps, enabling real-time CO₂ emissions calculation and tracking at the piece and product level. CO₂ emissions data are stored as additional "Quality Indication KPIs".
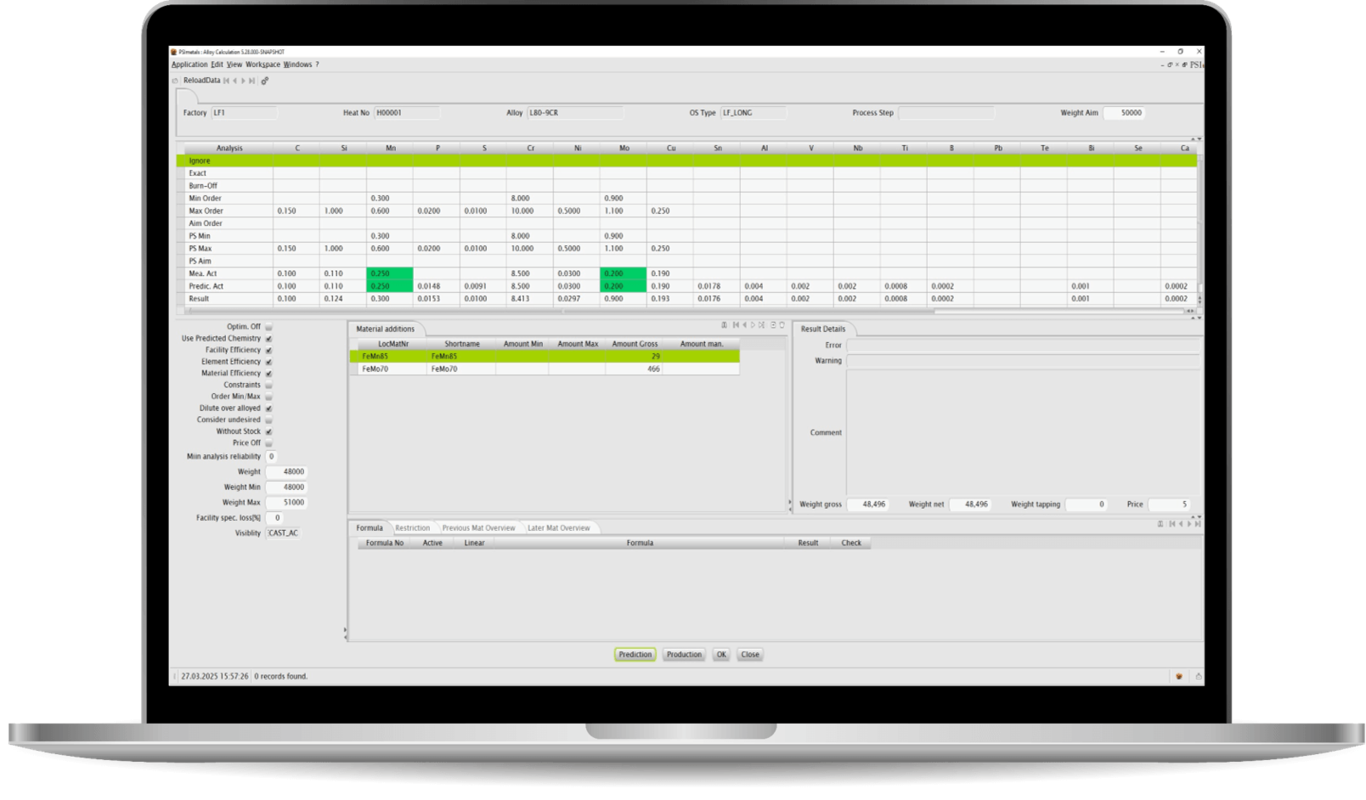
Charge and Alloying Model (ACM)
Using the specific meltdown energy and CO₂ footprint of raw materials, the heat’s total energy costs and carbon footprint can be calculated and minimized with an enhanced Charge and Alloying Model (ACM). The model is a component of PSImetals Production (Liquid) and supports optimized scrap and alloy procurement based on long-term heat planning.
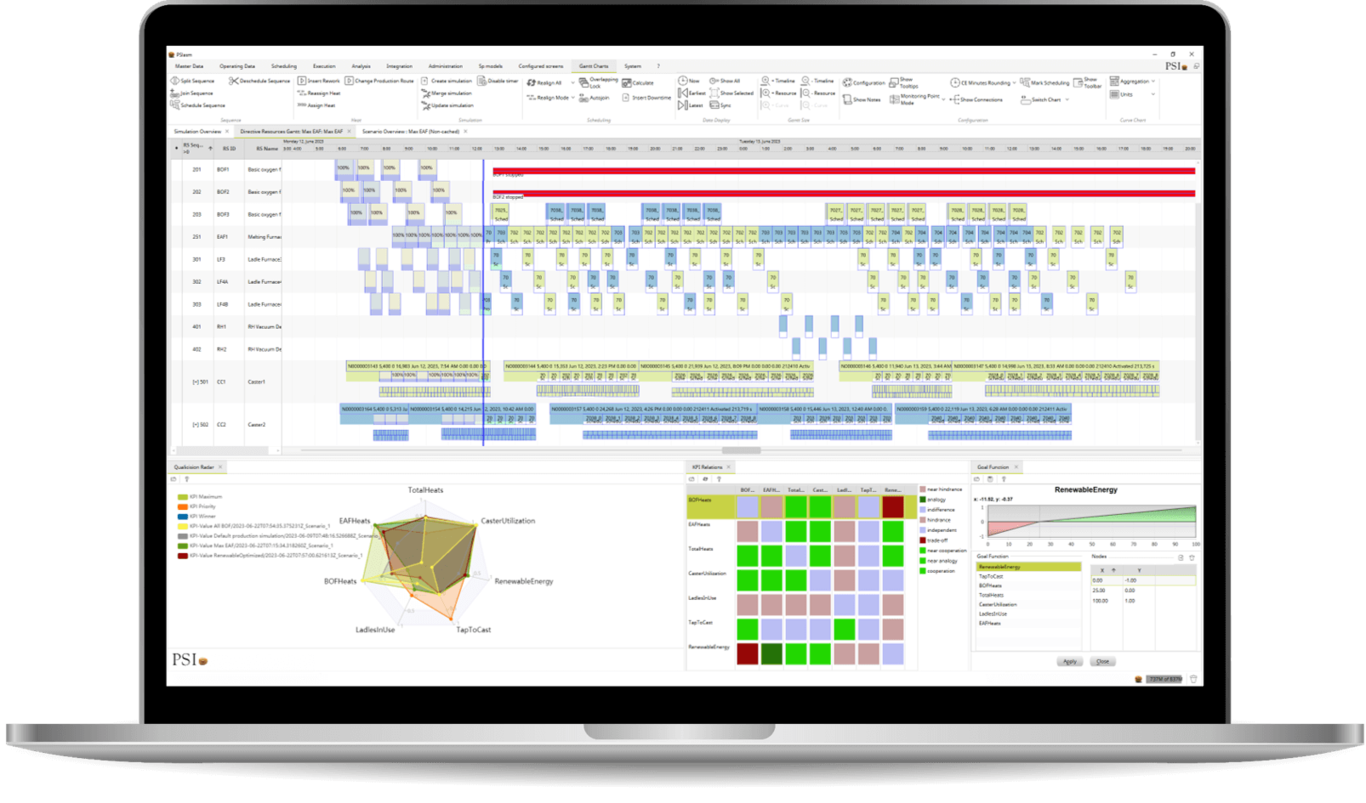
Production Planning and Scheduling
Raw materials and energy demands, along with resulting CO₂ emissions, are key parameters in rule-based Production Order elaboration (Order Dressing). This enables forecasting green KPIs like total energy consumption and CO₂ emissions, balancing them with productivity, quality, and cost targets for optimized production planning and execution. It also aligns energy demands with availabilities and supports the optimization of energy procurement, including day-ahead and intraday trading.
Whitepaper
Ready to lead the green revolution?
Download our exclusive whitepaper to learn how PSImetals can transform your production process for a greener future.
Discover how PSImetals supports decarbonization in the metal industry by:
- Replacing CO₂-intensive processes with greener alternatives
- Optimizing energy and material usage with AI-driven solutions
- Providing real-time tracking of greenhouse gas emissions
- Minimizing costs and carbon footprints through alloy & charge optimization
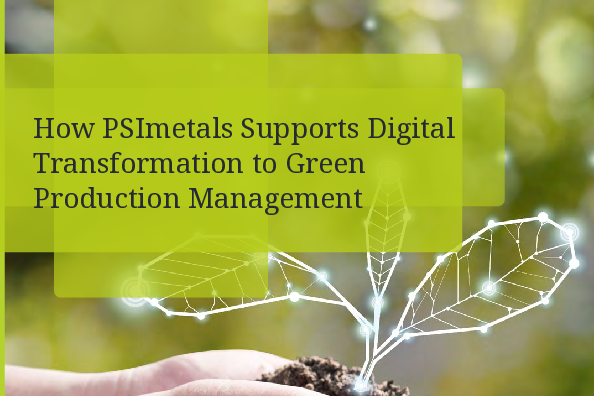